Top-Rated CMS Motors: Repair & Service
What are the critical components and applications of a specific type of motor? A comprehensive exploration of a particular motor design.
This type of electric motor, frequently employed in automated systems and machinery, relies on a particular configuration of components. Its design often prioritizes precise control, high efficiency, and consistent torque output. Examples include systems used in robotics, automated manufacturing, and specialized industrial equipment.
The motor's advantages stem from its carefully engineered structure. This may include specific stator designs, rotor materials, and precise control mechanisms. The resulting performance benefits often include high power density, low maintenance requirements, and the ability to function in challenging operational environments. The historical context involves advancements in motor technology, driving innovations in industries seeking enhanced automation and precision.
Moving forward, we will delve into the intricate details of motor design, examining the specifics of its structure, operation, and practical applications in industrial settings.
CMS Motors
Understanding the core components of a CMS motor system is crucial for effective application and maintenance. These elements interact to produce a specific output.
- Design
- Control systems
- Power efficiency
- Torque output
- Maintenance requirements
- Application suitability
A well-designed CMS motor emphasizes optimal power efficiency and consistent torque output. Control systems govern the motor's response, adapting to changing needs. Maintenance protocols are essential for prolonged operation. Application suitability determines the motor's proper placement within an automated system. Understanding the design principles and inherent limitations of the CMS motor architecture dictates proper integration and application. For example, a motor optimized for high-speed operation might be unsuitable for applications requiring consistent, low-speed torque. The synergy between all these aspects defines the motor's utility and reliability.
1. Design
The design of a CMS motor profoundly influences its performance characteristics, operational efficiency, and suitability for specific applications. Optimal design considers factors such as the material properties of the rotor and stator, the arrangement of windings, and the overall mechanical structure. A meticulously designed motor will exhibit reduced energy consumption, enhanced torque output, and extended operational lifespan. Conversely, a poorly designed motor may experience significant losses in efficiency, reduced power output, and potentially premature failure. For instance, an inadequate stator design could lead to excessive heat generation and reduced motor life.
Practical implications of a robust design extend beyond theoretical considerations. A motor designed for high-speed operation may necessitate a different winding configuration and potentially specialized materials to withstand the associated stresses. Conversely, a motor optimized for high torque at low speeds might employ a different rotor design. Understanding these design choices is critical for selecting the appropriate motor for a given application and ensuring its reliability in a specific environment. Examples include industrial automation where consistent torque at variable speeds is essential or in high-performance robotic systems where fast acceleration and deceleration are required.
In summary, the design of a CMS motor is a critical component determining its overall performance. Careful consideration of design elements is essential for optimal functionality. Addressing potential design flaws during the design phase can prevent costly issues in practical implementation. Understanding these relationships directly impacts selecting the right motor type for a given application, ultimately leading to improved reliability and efficiency in the system's operation.
2. Control Systems
Control systems are integral to the performance and reliability of CMS motors. Precise control dictates the motor's operational parameters, ensuring it functions within the desired specifications. Effective control mechanisms influence torque output, speed regulation, and overall efficiency. Deviations from optimal control parameters can lead to significant performance degradation, reduced lifespan, and potential hazards in applications that demand precision.
The importance of control systems in CMS motors is underscored by their role in maintaining consistent output in various applications. For instance, in automated manufacturing, precise speed and torque control are critical for maintaining production quality. Similarly, in robotic systems, intricate control algorithms regulate the motor's response to complex trajectories and demands. Failure to maintain precise control can result in jerky movements, inaccurate positioning, and ultimately, system failure. In industrial automation, control systems fine-tune the motor's output, reacting to fluctuations in load demands and ensuring consistent performance. This responsiveness is essential for maintaining production timelines and maximizing efficiency in dynamic environments.
Understanding the relationship between control systems and CMS motors is crucial for optimizing system performance and minimizing downtime. Advanced control algorithms and sophisticated sensor integration permit fine-tuned motor control, resulting in heightened efficiency and precision. Challenges arise when control systems fail to adapt to unexpected operational conditions or when the motor encounters unanticipated loads. Thorough testing and rigorous maintenance protocols are critical to mitigating risks and ensuring sustained performance. Effective control systems are essential for the safe and reliable operation of CMS motors within complex automated systems.
3. Power Efficiency
Power efficiency in CMS motors is paramount. Optimizing energy consumption directly impacts operational costs, environmental impact, and overall system performance. A motor's ability to convert electrical input into mechanical output with minimal loss is a key determinant of its utility in diverse applications. This section explores critical facets of power efficiency within CMS motors.
- Minimizing Energy Losses
Efficient CMS motors reduce energy dissipation through careful design and material selection. Minimizing resistance in windings, reducing friction in bearings, and employing advanced cooling techniques are crucial. High-efficiency motors translate to lower energy bills in industrial settings and contribute to a reduced carbon footprint. Examples include applications demanding extended operation, such as automated assembly lines or robotic systems, where significant energy savings translate to substantial cost reductions over time.
- Optimized Design for Efficiency
The design of CMS motors profoundly affects power efficiency. Elements such as stator construction, rotor configuration, and the choice of magnetic materials directly influence energy conversion and loss. Advanced computational modeling and optimization techniques play a crucial role in achieving desired efficiency levels. Examples are found in high-performance equipment where energy efficiency directly impacts overall system performance. Precise design choices in such motors can directly affect the sustainability of entire production processes.
- Control Systems and Efficiency
Control systems play a vital role in maximizing power efficiency in CMS motors. Sophisticated algorithms optimize operation by regulating speed and torque based on the instantaneous load. Variable frequency drives (VFDs) are frequently employed to adjust motor speed, minimizing energy expenditure when demands are low. Examples such as industrial equipment where operating conditions fluctuate can benefit from this variable control to enhance efficiency. Optimal control ensures energy use matches production needs.
- Operational Environment and Efficiency
The operational environment significantly influences the power efficiency of CMS motors. Factors such as ambient temperature, dust accumulation, and vibration can negatively affect performance. Proper maintenance, including regular inspections and cleaning, ensures optimal conditions, which leads to enhanced power efficiency. Environmental monitoring and mitigation strategies further optimize performance. Examples include industrial settings susceptible to extreme temperatures or harsh conditions; well-maintained motors in such environments demonstrate a longer operational lifespan and higher efficiency over time.
Ultimately, superior power efficiency in CMS motors translates to reduced operational costs, minimized environmental impact, and increased overall system reliability. The considerations outlined above ensure optimized energy conversion, contributing to sustainable and cost-effective applications.
4. Torque Output
Torque output is a critical performance metric for CMS motors, directly influencing their suitability for various applications. A motor's ability to generate torquethe rotational forcedetermines its capacity to drive machinery, lift loads, or perform other mechanical tasks. Understanding torque output's nuances is essential for selecting the appropriate motor for a given task.
- Design Considerations
The design of the CMS motor significantly impacts its torque output. Factors such as the number of windings, the size and material of the rotor, and the arrangement of magnetic fields all influence the magnitude and consistency of torque. Motors intended for high-torque applications necessitate specific design elements; these elements may differ from designs prioritized for high-speed operation. Specialized materials for rotors and stators might be used to improve the motor's performance within a specific application.
- Load Requirements and Torque
The torque required by a specific application dictates the appropriate selection of a CMS motor. High-torque applications, such as industrial conveyors or heavy-lifting mechanisms, demand motors capable of generating substantial rotational force. Conversely, lower-torque applications, like small robotic manipulators or precision positioning systems, necessitate motors with controlled torque outputs. Matching the motor's torque capability to the load requirements is fundamental for efficient and reliable operation.
- Control Systems and Torque Regulation
Control systems enable precise regulation of torque output, crucial for tasks needing variable torque or precise control. Variable frequency drives (VFDs) are often employed to adjust motor speed and, consequently, the generated torque. In applications demanding smooth acceleration and deceleration, precise torque regulation through control systems is essential for performance and stability. This feature is especially important in applications such as automated manufacturing or robotics where precise movements and forces are required.
- Operational Efficiency and Torque
The relationship between torque output and efficiency is often complex. High-torque motors may have reduced efficiency in lower-load conditions, while the reverse may also be true. Optimizing design and control systems allows for both high torque output and acceptable energy consumption. Finding the optimal balance between torque output and energy consumption is crucial for cost-effectiveness and sustainability within a system. In many cases, the use of advanced controls and algorithms allows the motor to adjust its torque output in real-time to meet changing needs, maintaining high efficiency overall.
In summary, torque output is not a singular aspect of CMS motors but a multifaceted performance characteristic that interacts with design, control systems, operational requirements, and efficiency. The precise specification of torque output is crucial for the reliable and efficient operation of systems integrating CMS motors. Selecting the appropriate motor type necessitates careful consideration of all the aforementioned factors. Careful consideration of torque output in design and control is essential for the smooth and efficient function of the overall system.
5. Maintenance Requirements
Maintenance requirements for CMS motors are not merely a secondary concern but a fundamental aspect of operational reliability and longevity. Proactive maintenance directly impacts the motor's lifespan, efficiency, and safety. Neglecting these requirements can lead to premature failure, costly repairs, and potentially hazardous situations in critical applications. A well-maintained CMS motor functions consistently, minimizing downtime and maximizing operational efficiency.
The importance of regular maintenance stems from the inherent wear and tear of mechanical components within the motor. Components like bearings, windings, and seals degrade over time due to friction, thermal stress, and environmental factors. Regular inspections, lubrication, and cleaning help mitigate these issues, extending the motor's operational lifespan. Examples include industrial automation, where uninterrupted operation is essential. A well-maintained motor in such an environment translates to fewer production disruptions, contributing directly to enhanced efficiency and profitability. Furthermore, neglecting maintenance can result in catastrophic failures, especially in safety-critical applications. This risk is further magnified when the motor is part of a larger automated system, where failure can have cascading effects. Proper maintenance protocols reduce these risks and ensure the smooth operation of connected equipment.
Understanding the link between maintenance and CMS motor performance is crucial for effective system management. Proactive maintenance schedules, comprehensive documentation of maintenance activities, and training for personnel responsible for maintenance are all essential aspects of long-term motor health. The avoidance of preventable failures through vigilant maintenance practices translates to reduced operating costs and a minimized environmental impact. The avoidance of preventable failures ensures the reliable functioning of the entire system. A proactive approach to motor maintenance not only extends the life of the CMS motor itself but also significantly contributes to the overall success of any system it powers. Failing to recognize this can lead to substantial financial losses, increased downtime, and the potential for safety incidents.
6. Application Suitability
The suitability of a particular type of motor for a specific application is a critical factor influencing its performance, efficiency, and longevity. Matching motor characteristics to application requirements is paramount. Factors such as the required torque, speed, load profile, operating environment, and expected lifespan all influence the selection process. Improper selection can lead to reduced performance, premature failure, and increased operational costs. A nuanced understanding of application suitability is essential to avoid these issues. For example, a motor designed for high-speed, low-torque applications may be unsuitable for an application demanding high torque at a constant speed. Conversely, a high-torque motor might be inefficient in a low-torque application.
Practical applications highlight the importance of matching specific motors to particular needs. In automated manufacturing, high-precision positioning systems require motors with precise speed and torque control. These motors often integrate complex control systems. Similarly, industrial machinery employing heavy loads necessitates motors with substantial torque capacity. Selecting the correct motor directly impacts the efficiency and reliability of the overall system. Furthermore, operational environment considerations, such as temperature extremes or exposure to corrosive substances, require specific motor types to withstand the conditions. For example, in corrosive environments, specialized materials are critical for motor durability and functionality.
In conclusion, application suitability is not merely an optional consideration but a fundamental aspect of selecting and utilizing CMS motors. Careful evaluation of application demands, alongside the technical specifications of potential motors, is crucial for optimizing performance and longevity. Matching the specific characteristics of the motor to the precise needs of the application ensures the system operates efficiently, reliably, and safely. The selection process should incorporate a thorough understanding of the interaction between the motor and its surroundings to ensure long-term viability and cost-effectiveness within the specific application.
Frequently Asked Questions (CMS Motors)
This section addresses common inquiries regarding CMS motors, offering clarity and insight into various aspects of these specialized electric motors. Comprehensive answers are provided to promote understanding and facilitate informed decision-making.
Question 1: What distinguishes CMS motors from other types of motors?
CMS motors exhibit specific design characteristics that differentiate them. These may include specialized stator windings, optimized rotor materials, and unique control systems, yielding performance advantages in specific application contexts. A critical distinction is typically found in their tailored control systems enabling highly precise speed and torque regulation.
Question 2: What are the typical applications of CMS motors?
CMS motors are often utilized in demanding applications necessitating precise control and consistent torque. Examples include high-precision robotics, automated manufacturing, and sophisticated industrial machinery where precise positioning and smooth operation are essential. These applications leverage the high-performance traits inherent in this type of motor design.
Question 3: How does the design of a CMS motor influence its efficiency?
Motor design significantly impacts efficiency. Specific design features, such as material choices and winding configurations, influence energy conversion and loss. Sophisticated designs optimize energy usage, reducing operational costs and environmental impact. Well-designed motors demonstrate higher efficiency through minimizing energy losses during operation.
Question 4: What factors influence the maintenance requirements of CMS motors?
Maintenance demands vary based on application and operational conditions. Environmental factors, such as extreme temperatures or exposure to contaminants, can impact component longevity and require more rigorous upkeep. Regular inspections and proactive maintenance procedures are vital for extending the operational life and ensuring reliable function. The complex nature of CMS motors requires skilled maintenance personnel to address specific design features.
Question 5: How can the operational efficiency of a CMS motor be maximized?
Maximizing efficiency hinges on careful selection and configuration of the motor, optimal control strategies, and adherence to maintenance protocols. Selecting the appropriate motor for the intended application, utilizing advanced control algorithms, and implementing stringent maintenance plans can significantly enhance energy use and minimize operational costs. Systematically addressing potential energy loss points directly impacts efficiency gains.
In summary, CMS motors offer specialized performance characteristics, driving advancements in precise automation. Understanding these features and associated considerations allows for informed decision-making in the selection and implementation of this technology within various applications.
Moving forward, the following sections will delve deeper into design elements, operational principles, and specific application considerations.
Conclusion
This exploration of CMS motors highlights the intricate interplay of design, control systems, efficiency, torque, maintenance, and application suitability. The analysis demonstrates that a comprehensive understanding of these elements is critical for optimizing performance, minimizing operational costs, and maximizing the lifespan of these complex motors. Key considerations include the direct correlation between motor design and torque output, the pivotal role of control systems in achieving precise performance, and the importance of proactive maintenance for sustained operational reliability. The selection of a CMS motor for a particular application must carefully weigh load requirements, environmental factors, and projected operational lifespan. Efficiency optimization through appropriate design, control, and maintenance practices is demonstrably crucial for sustained cost-effectiveness.
The advancements in CMS motor technology continue to drive innovations in automation, precision machinery, and related fields. Careful consideration of these design and operational factors remains paramount for ensuring both reliable performance and long-term viability in modern industrial contexts. Future research and development likely will continue to refine these technologies, potentially leading to more efficient and advanced applications within these critical sectors.
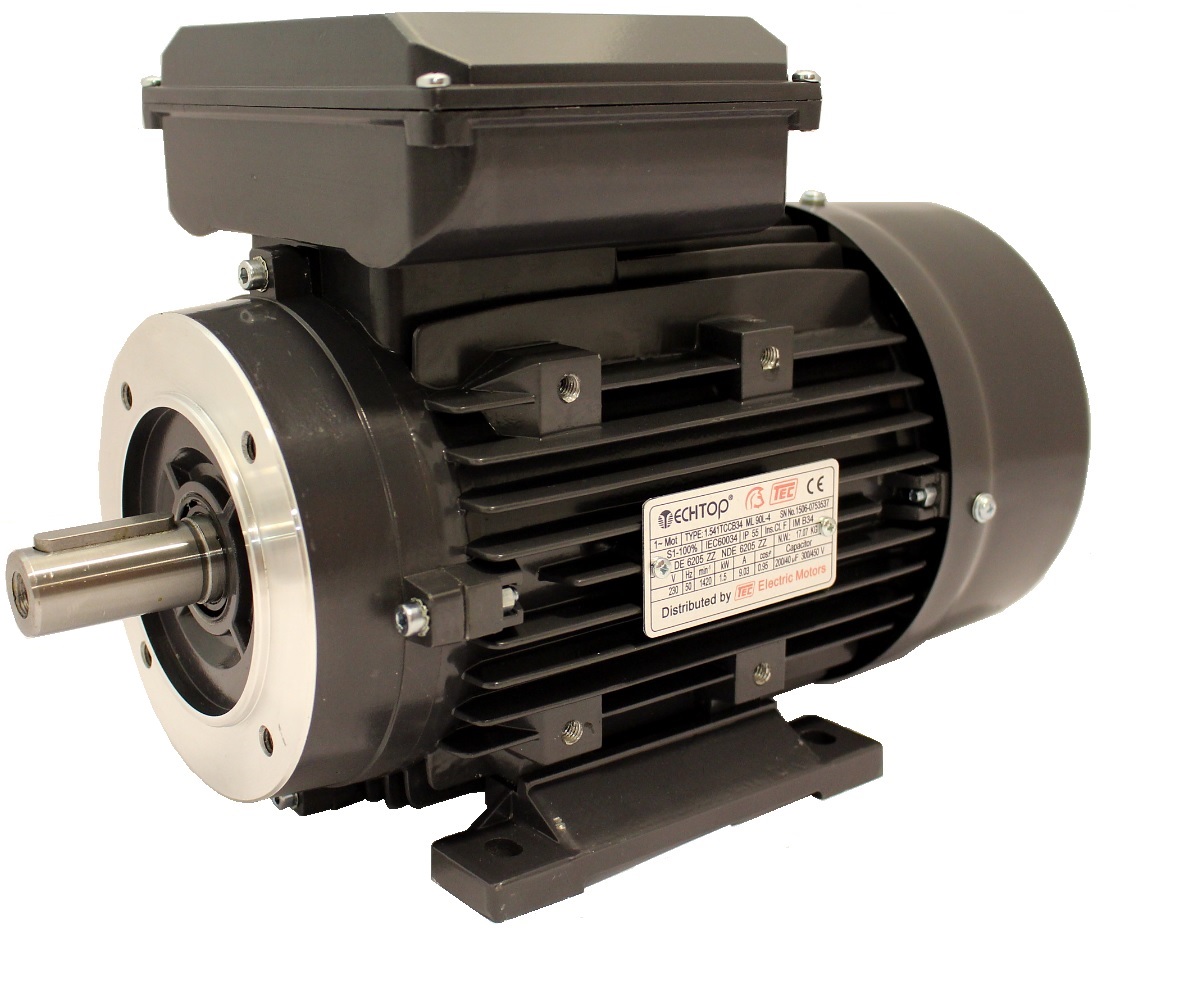
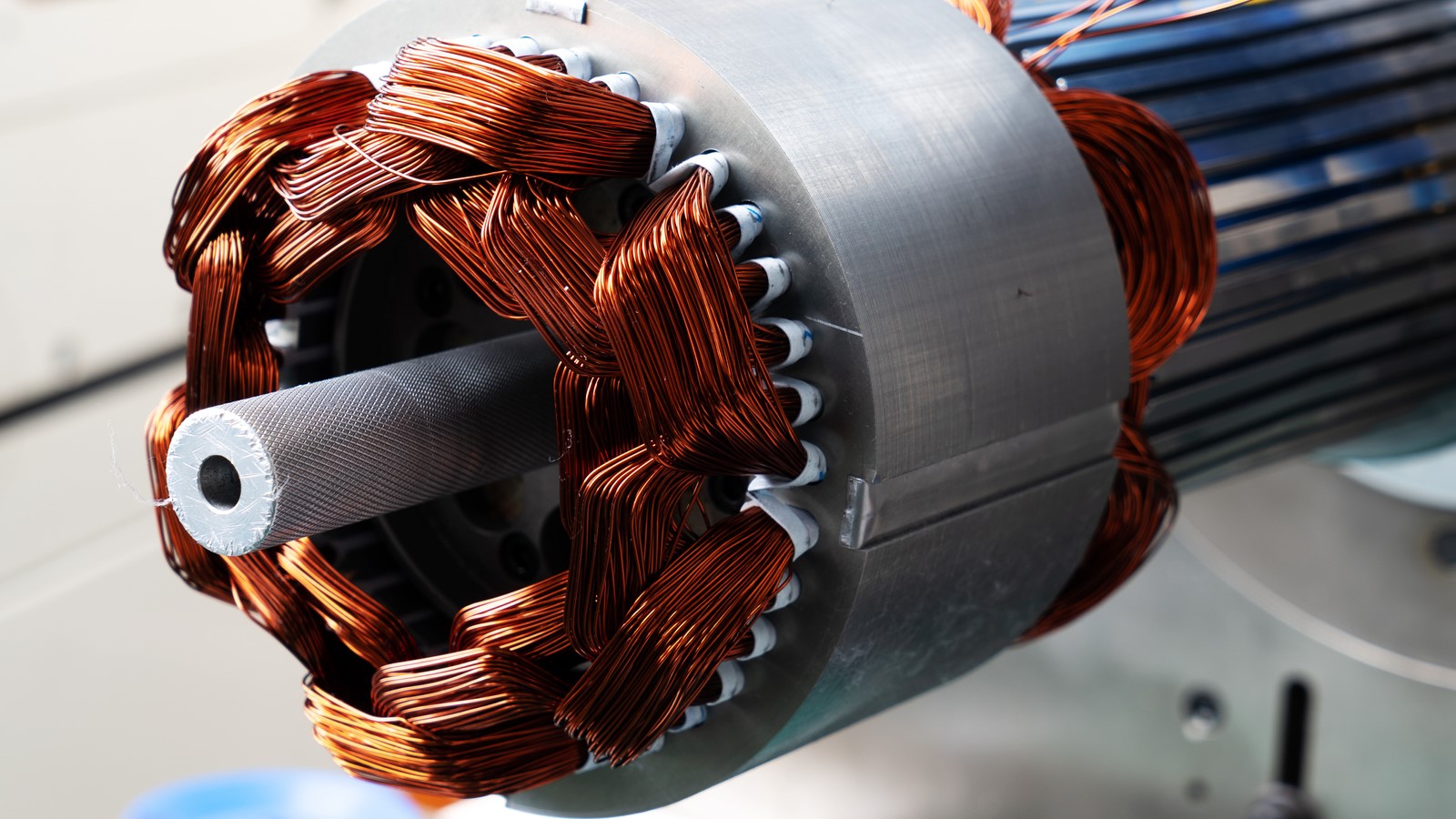

Detail Author:
- Name : Esmeralda Pfannerstill
- Username : elwin38
- Email : prempel@bode.info
- Birthdate : 1981-03-09
- Address : 6079 Greenholt Corner Ellismouth, CO 81927
- Phone : (419) 858-5382
- Company : Kemmer-Eichmann
- Job : Paralegal
- Bio : Provident qui iure saepe autem iste quo. At qui provident animi consequuntur quis sunt repellendus. Asperiores pariatur eius quod aliquid et iste magni.
Socials
linkedin:
- url : https://linkedin.com/in/rosalia_id
- username : rosalia_id
- bio : Consequatur ut atque dolores aut laboriosam.
- followers : 3768
- following : 1851
twitter:
- url : https://twitter.com/hower
- username : hower
- bio : Placeat eum quisquam enim maiores ex. Repudiandae omnis odio velit ea. Quas et vel qui voluptas veniam incidunt.
- followers : 5871
- following : 1029
tiktok:
- url : https://tiktok.com/@rosalia_real
- username : rosalia_real
- bio : Ut architecto aut et eos distinctio est itaque.
- followers : 3703
- following : 1774
facebook:
- url : https://facebook.com/rosalia_howe
- username : rosalia_howe
- bio : Et quia officiis vel odio magnam. Et officiis illo in et quod.
- followers : 5474
- following : 586
instagram:
- url : https://instagram.com/rosaliahowe
- username : rosaliahowe
- bio : Porro consequatur consequatur rem dolorem. Molestiae laudantium facere et possimus.
- followers : 4366
- following : 778