High-Quality Altium Cabinets & Storage Solutions
What are the key features and applications of these enclosed systems used in electronic design?
These enclosed systems, often used in electronic design, provide a protective shell for circuit boards and other components. They are frequently customizable, allowing for tailored configurations to suit specific project needs. Examples include enclosures for test equipment, small appliances, or specialized electronic devices requiring containment. They are designed to prevent environmental hazards such as dust, moisture, and mechanical stress from affecting the inner workings.
The importance of these enclosures stems from their role in protecting sensitive electronics. Thorough design considerations guarantee electrical safety and operational reliability. Proper sealing and component placement inside the enclosure are essential. Their use directly impacts the longevity and performance of the housed electronics. Additionally, these systems can often meet industry or regulatory standards, ensuring the quality and safety of the contained equipment.
- The Ultimate Guide To Indian Adult Films Uncensored And Unforgettable
- Exploring The Life And Achievements Of Oliver Mclanahan Phillips
Moving forward, we will explore the specific considerations in selecting and configuring these protective systems for various electronics projects. Factors such as size, material, and required certifications will be examined.
Altium Cabinet
Understanding the essential components of an enclosure system is critical for successful electronic design. These enclosures protect sensitive components and ensure reliable operation.
- Protection
- Customization
- Compliance
- Material
- Size
- Functionality
Enclosures, often referred to as cabinets, provide critical protection against environmental factors. Customization allows for tailoring the enclosure to specific devices, while compliance with industry standards ensures safety and reliability. Selecting appropriate materials and sizes is essential to guarantee both protection and functionality. Consider, for example, the need for heat dissipation in a server cabinet versus the protection of a sensitive sensor. The specific functions of the enclosed device directly influence the type of enclosure required.
1. Protection
The primary function of an enclosure, or cabinet, is protection. This protection encompasses various aspects, safeguarding the internal components from a multitude of potential threats. Environmental hazards such as dust, moisture, and extreme temperatures are mitigated through appropriate enclosure design and materials. Mechanical stresses, including vibration and impact, are also addressed through robust construction. Furthermore, protection often includes electrical isolation to prevent short circuits and ensure the safe operation of the enclosed equipment. Adequate shielding against electromagnetic interference (EMI) and radio frequency interference (RFI) is another critical protective element, vital in sensitive electronic environments.
The importance of this protection is evident in countless real-world applications. In industrial settings, enclosures safeguard machinery and control systems from harsh operating conditions. In medical devices, protection ensures safety and reliability. Electronic equipment in automobiles, for instance, needs protection against vibration, temperature variations, and potential physical damage. Without effective protection, equipment failure, costly repairs, and potential safety hazards would arise. The careful selection of materials, design features, and sealing methods directly relates to the effectiveness of protection, highlighting the significance of understanding these connections for optimal performance and reliability.
In conclusion, the protection afforded by an enclosure is paramount to its operational success. The specific nature of the protection required varies greatly depending on the application. Comprehensive understanding of potential threats and the subsequent design considerations are crucial for delivering an enclosure that effectively safeguards the enclosed components and ensures dependable operation. This fundamental aspect shapes the overall design, cost, and reliability of any enclosed electronic system.
2. Customization
Customization in enclosure design, a critical component of effective electronic systems, allows for tailored solutions. This adaptability addresses diverse needs across varied applications. A standardized, "one-size-fits-all" approach is often insufficient. The intricate requirements of specific devices, from compact sensor arrays to high-powered servers, demand specific configurations. Enclosures must accommodate component placement, heat dissipation, and regulatory compliance; customization allows precise tailoring for optimal performance and functionality. This adaptability necessitates detailed consideration of the internal components and external factors influencing the enclosed system.
Customization in enclosure design is not merely cosmetic. It's a fundamental element impacting performance, safety, and cost-effectiveness. Consider a medical device requiring compact dimensions and stringent electromagnetic shielding. A customized enclosure, meticulously designed to meet these criteria, ensures optimal functionality and regulatory compliance, preventing interference and guaranteeing reliability. Contrast this with an industrial control panel, requiring robustness and heat dissipation capabilities. A tailored enclosure, featuring specialized ventilation and reinforced structural elements, would be necessary for safe and consistent operation. Customization, therefore, is vital in meeting the particular demands of each application.
In conclusion, the ability to customize enclosures is a crucial aspect of modern electronic design. Tailored solutions provide the flexibility necessary to address the unique needs of diverse applications. This adaptability ensures optimal performance, safety, and reliability while minimizing costs associated with unnecessary features or components. Understanding and leveraging customization capabilities in enclosure design is essential for creating robust, effective, and cost-efficient electronic systems. The practical and safety implications of this understanding are profound.
3. Compliance
Compliance requirements play a critical role in the design and deployment of enclosures, often referred to as cabinets. Meeting these standards is essential for the safe and reliable operation of enclosed electronic systems and ensuring they meet regulatory and safety standards.
- Electrical Safety Standards
Enclosures must comply with electrical safety standards to prevent electrical hazards. These standards dictate insulation requirements, grounding procedures, and the maximum allowable voltage and current levels. Failure to meet these standards could lead to electrical shocks, fires, or equipment malfunctions. For example, medical equipment enclosures require stringent compliance with specific regulations related to patient safety. Similarly, industrial control panel enclosures must adhere to standards ensuring the safety of personnel working in proximity.
- Environmental Regulations
Enclosures must meet environmental regulations related to material usage, electromagnetic compatibility (EMC), and emissions. This encompasses restrictions on the use of hazardous substances like lead or mercury. The design must also consider the necessary shielding and filtering to reduce electromagnetic interference and prevent emissions exceeding regulatory limits. For instance, enclosures used in the telecommunications industry must adhere to EMC standards to prevent disruptions to communication networks.
- Mechanical Requirements
Compliance with mechanical standards ensures the structural integrity and durability of the enclosure. Standards related to impact resistance, vibration tolerance, and temperature resistance are critical for reliable performance in diverse operating environments. This is especially important for enclosures used in vehicles, industrial machinery, or other environments exposed to significant mechanical stresses. Failure to meet these standards could result in the enclosure's deformation or failure under stress, potentially damaging the enclosed equipment.
- Industry-Specific Standards
Many industries have specific standards for enclosures. These standards may address particular safety concerns or performance requirements specific to the intended application. For example, aerospace enclosures have stringent requirements for weight, material selection, and environmental protection. Meeting these industry-specific standards is vital for assuring quality and compatibility within the respective industry's operational contexts.
Compliance considerations are intrinsically linked to the overall design and functionality of an enclosure. Selecting appropriate materials, designing effective seals, and considering the potential environmental impacts are all crucial aspects. Meeting compliance requirements ensures the safety and reliability of the enclosed electronic equipment. Failure to adhere to regulations can lead to serious consequences, including product recalls, fines, and safety hazards. Thorough understanding and proactive compliance with these various standards are essential for creating safe, reliable, and robust enclosures.
4. Material
Material selection is paramount in the design of enclosures, frequently referred to as cabinets. The properties of the chosen material directly impact the enclosure's performance, safety, and cost-effectiveness. Factors like strength, durability, resistance to environmental stresses, and electrical conductivity are crucial considerations. The inherent characteristics of the material dictate the enclosure's ability to withstand various operating conditions and maintain the integrity of the housed components.
Diverse materials are employed, each with unique advantages and limitations. Metals, such as steel and aluminum, offer high strength and durability, suitable for demanding industrial environments. Plastics, however, possess advantages in terms of lightweight construction and cost-effectiveness, making them suitable for consumer electronics. Choosing the right material for a specific application depends on a careful evaluation of factors like expected mechanical stress, operating temperature, and electrical requirements. For example, an enclosure housing sensitive electronics in a harsh industrial environment necessitates a material offering exceptional protection against corrosion and mechanical shocks. Conversely, a lightweight enclosure for portable devices might prioritize a robust plastic with good thermal properties over a more expensive metal. Material selection should also account for environmental concerns, with environmentally friendly materials becoming increasingly significant in recent design practices.
Understanding the interplay between material properties and enclosure performance is vital. A material's resistance to chemicals, moisture, and temperature fluctuations directly impacts the lifespan and reliability of the enclosed equipment. Moreover, material choices influence the cost of manufacturing and the overall efficiency of the enclosure. The correct selection optimizes the design's safety, functionality, and economic viability. Carefully considering these aspects ensures the enclosure reliably meets its intended purpose, thereby contributing to the overall success of the designed system. Consequently, informed material selection is a fundamental element for developing robust, practical, and cost-effective enclosures.
5. Size
Enclosure size is a critical design parameter directly influencing the performance and functionality of electronic cabinets. Proper sizing is crucial for accommodating internal components, ensuring efficient heat dissipation, and maintaining the intended operational parameters of the enclosed equipment. Inadequate size can lead to performance limitations, overheating, and even damage to components. Conversely, excessive size results in unnecessary bulk, increased weight, and potentially higher production costs.
- Component Accommodation
Adequate internal space is essential for properly positioning components, such as circuit boards, connectors, and other crucial elements. Insufficient space can lead to component overcrowding, impacting airflow and heat dissipation. Improperly placed components can also cause interference and damage during assembly and operation. A well-designed enclosure ensures sufficient space for all components and facilitates efficient cable management, contributing to the overall operational reliability.
- Heat Dissipation
Enclosure size significantly affects heat dissipation. Larger enclosures often offer more volume for heat transfer, crucial for applications involving components generating substantial heat. Sufficient space allows for proper airflow, facilitating convective cooling and preventing overheating of components. Conversely, a small enclosure may not provide sufficient space for adequate heat dissipation, resulting in temperature increases that could damage components and compromise performance. Appropriate heat dissipation is paramount for reliable long-term operation.
- Manufacturing and Assembly
Size directly impacts the ease of manufacturing and assembly processes. A meticulously designed enclosure size simplifies the integration of components and assembly operations. Optimized dimensions facilitate efficient handling during assembly, reducing potential errors and increasing production throughput. Conversely, poorly designed enclosure dimensions can make assembly complex, time-consuming, and prone to errors. Considerations for tooling, access for assembly personnel, and component manipulation are all influenced by enclosure dimensions.
- Cost Implications
Larger enclosures generally translate to increased material costs and a larger footprint, impacting overall project economics. Conversely, smaller enclosures may reduce material expenses, but could necessitate more complex component placement strategies or increased costs for specialized components to accommodate the tighter space. Optimizing size considerations within the context of budgetary constraints ensures cost-effectiveness without sacrificing performance. Strategic sizing decisions significantly affect the project's financial feasibility.
In conclusion, size is an integral part of enclosure design. Careful consideration of the relationship between size, component accommodation, heat dissipation, manufacturing, and cost is critical for creating efficient, reliable, and cost-effective electronic cabinets. A well-designed enclosure size not only accommodates internal components but also optimizes performance, reduces maintenance needs, and improves the overall system's operational lifespan.
6. Functionality
Functionality, in the context of electronic enclosures (often called cabinets), is not merely about aesthetics but about the precise, intended role the enclosure plays in a system's overall operation. It encompasses the interplay between the enclosure's design, its internal components, and its operational environment. Understanding this interplay is essential to creating a cabinet that reliably fulfills its purpose.
- Internal Component Integration
The enclosure must accommodate internal componentscircuit boards, connectors, and other hardwarein a secure, organized, and efficient manner. Proper placement, accessibility for maintenance, and allowance for airflow for thermal management are all crucial facets. Optimal routing of cables and wiring ensures effective signal transmission and reduces potential interference. Real-world examples of this include the precise placement of circuit boards in server racks or the orderly arrangement of components in a medical device enclosure.
- Environmental Protection
The enclosure's functionality extends to environmental protection. Its design should safeguard against moisture, dust, and physical shocks. The enclosure's materials, seals, and overall construction are key factors influencing its ability to withstand the operational environment. This is vital in applications ranging from industrial control panels exposed to harsh weather to the sensitive circuitry within portable devices. The choice of materials, such as their resistance to chemicals or temperature variations, is a critical factor.
- Thermal Management
Effective thermal management is often a critical aspect of cabinet functionality. Components generate heat, and proper ventilation, heat sinks, and material selection are vital to preventing overheating and component failure. This aspect is particularly important in enclosures housing power electronics or those operating in demanding environments where temperatures fluctuate. This functionality is illustrated in power supplies and high-performance computing equipment where proper cooling is vital for stable performance.
- Accessibility and Maintainability
A well-designed enclosure facilitates easy access for maintenance and repair. Removable panels, standardized access points, and clear labeling simplify troubleshooting and component replacement. This directly influences the equipment's long-term reliability and operational efficiency. This is illustrated in the design of industrial control panels and server cabinets where regular maintenance is a requirement for optimal uptime.
In summary, the functionality of an enclosure (or cabinet) is a multifaceted concept directly tied to the successful operation of the housed electronic equipment. Considering these componentsinternal component integration, environmental protection, thermal management, and accessibilityresults in a cabinet that not only safeguards the equipment but also ensures long-term reliable performance.
Frequently Asked Questions about Enclosures
This section addresses common questions concerning enclosures, often called cabinets, used in electronic design. Clear answers are provided to clarify crucial aspects of these protective systems.
Question 1: What factors influence the choice of enclosure material?
The selection of enclosure material is heavily dependent on the intended application and operating environment. Key factors include: resistance to environmental stresses (like chemicals, moisture, and temperature fluctuations); mechanical strength and durability; electrical conductivity or insulation requirements; thermal conductivity for effective heat dissipation; and cost-effectiveness. Different materials possess varying combinations of these properties, and selecting the appropriate one is essential for optimal performance and longevity.
Question 2: How does enclosure size affect thermal management?
Enclosure size directly impacts thermal management. A larger enclosure typically provides more space for heat dissipation, allowing for better airflow and more efficient convective cooling. Conversely, a smaller enclosure might struggle to adequately dissipate heat generated by components, potentially leading to overheating. The balance between component density, heat generation, and available cooling space dictates the appropriate enclosure size for optimal thermal performance.
Question 3: What standards and regulations must enclosures meet?
Enclosures must conform to various safety and performance standards, depending on the intended use and region. These often encompass electrical safety regulations (such as insulation and grounding requirements); environmental standards (such as restrictions on hazardous materials and emissions); and mechanical standards (such as impact resistance and vibration tolerance). Failure to comply can result in product recalls, legal issues, and safety hazards.
Question 4: How important is customization in enclosure design?
Customization is crucial. A one-size-fits-all approach often proves inadequate. Specific device requirements, including component placement, heat dissipation needs, and adherence to regulatory standards, necessitate tailored solutions. Customization ensures optimal functionality, enhances safety, and ensures compliance with particular application needs.
Question 5: What are the typical applications for enclosures?
Enclosures are utilized in a wide range of applications. These include industrial equipment, medical devices, automotive components, and consumer electronics. The specific function of the enclosed system dictates the necessary enclosure properties, including protection, customizability, and compliance with applicable standards. Appropriate material selection, size, and thermal management design are critical considerations.
Understanding these factors allows for the selection and implementation of enclosures that deliver optimal performance, safety, and reliability. Choosing the correct enclosure for a specific application is essential for success.
Moving forward, let's delve deeper into the specific types of enclosures available and the factors to consider when selecting one for a particular project.
Conclusion
This exploration of electronic enclosures, often referred to as cabinets, highlights the multifaceted nature of their design and application. Key considerations include the critical need for robust protection against environmental factors, the importance of customizable designs to meet specific needs, compliance with industry standards to ensure safety and reliability, and the influence of material selection and size on overall performance. The functionality of an enclosure encompasses internal component integration, environmental protection, thermal management, and accessibility, each crucial for ensuring the longevity and dependability of housed equipment. Careful evaluation of these factors is essential for creating effective and cost-efficient electronic systems.
In conclusion, the selection and implementation of suitable enclosures is paramount in numerous applications. Understanding the nuances of enclosure design, materials, and regulatory considerations enables the development of resilient and reliable electronic systems, contributing to enhanced safety, improved performance, and long-term operational efficiency. A thorough understanding of these concepts empowers informed decision-making throughout the product design lifecycle, ultimately leading to more robust, cost-effective, and dependable technological solutions.
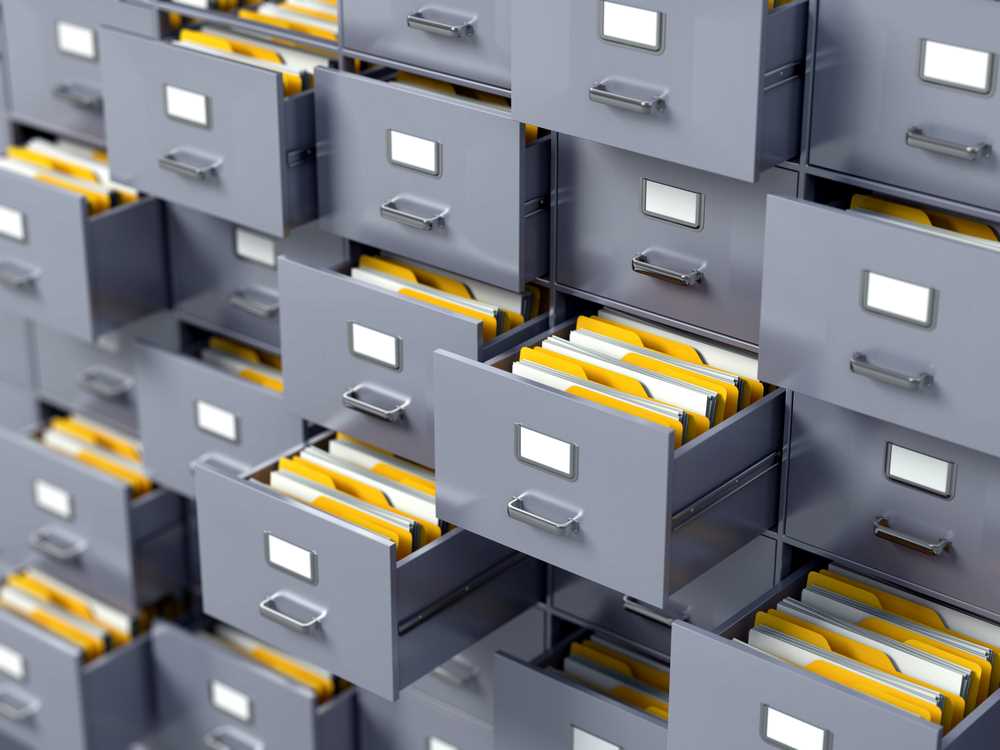
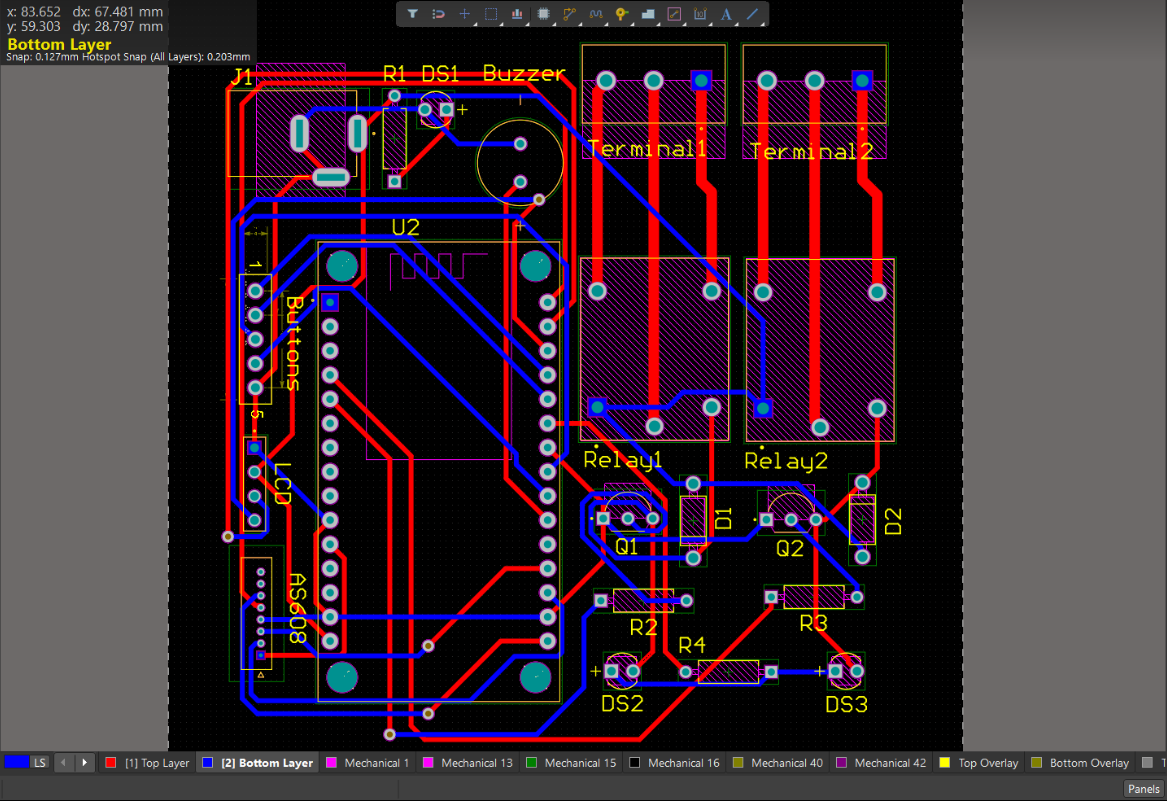
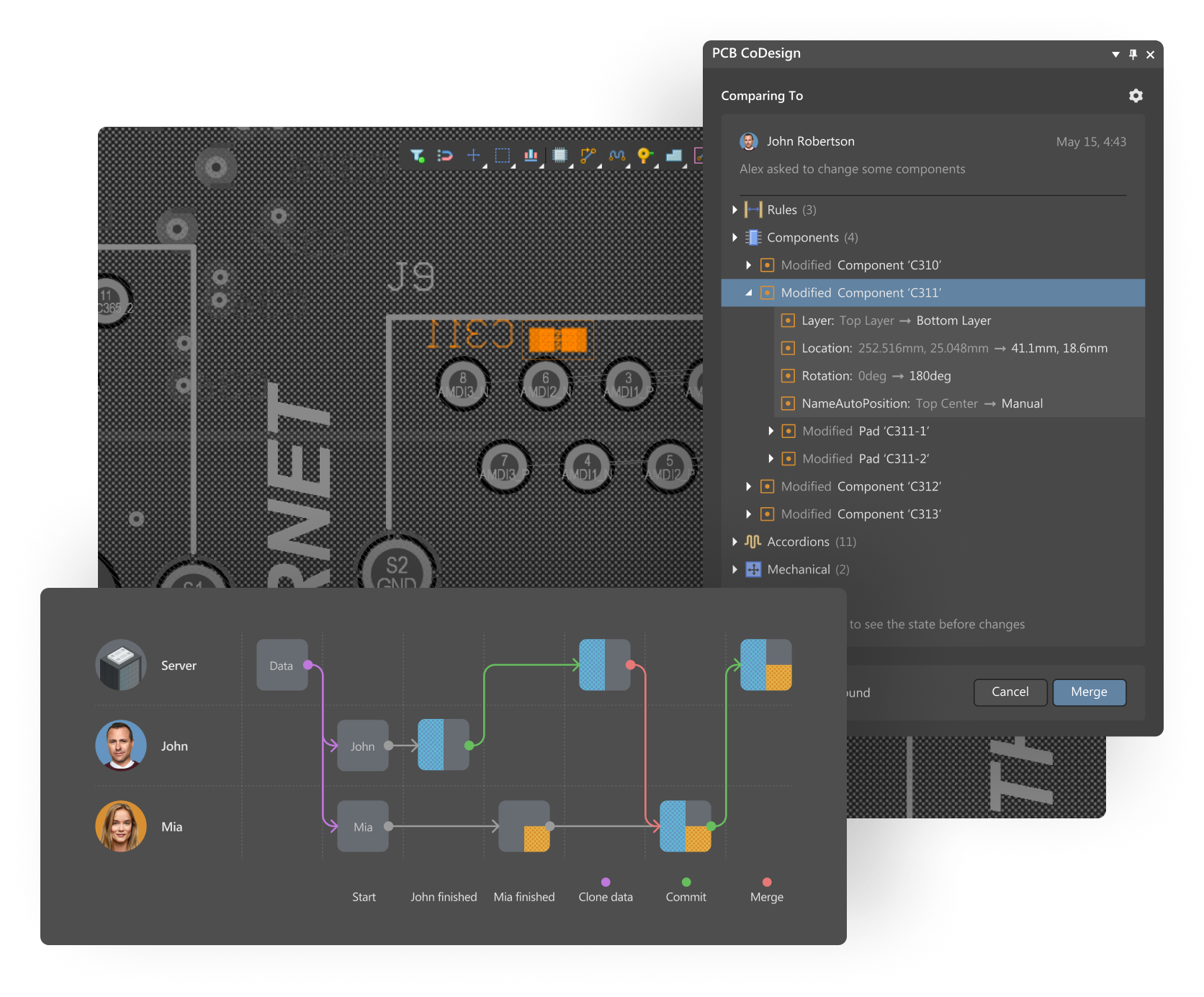
Detail Author:
- Name : Shanna Hammes
- Username : armani.kreiger
- Email : bgreenholt@steuber.org
- Birthdate : 1976-02-01
- Address : 44132 Lubowitz Fall Apt. 289 Feeneyville, IA 23509
- Phone : +1-785-398-5809
- Company : Kassulke LLC
- Job : Typesetter
- Bio : Adipisci optio voluptas aut est dolorem. Blanditiis quam dolores eos beatae. Molestias quibusdam qui modi enim similique ad exercitationem.
Socials
instagram:
- url : https://instagram.com/pierce_id
- username : pierce_id
- bio : Repellat similique cumque et et hic aut molestiae. Incidunt sit et architecto perferendis.
- followers : 6750
- following : 2203
facebook:
- url : https://facebook.com/lowe2016
- username : lowe2016
- bio : Quia similique dolorem alias vero est commodi commodi.
- followers : 3902
- following : 104