Fast Pace Printing: High-Quality Prints Delivered
How does adjusting the speed of a printing process affect output quality and efficiency? A thorough understanding of print speed control is crucial for optimized printing operations.
Adjusting the speed at which a printing press operates is a fundamental aspect of print production. This control variable directly impacts the quality of the final output and the overall efficiency of the printing process. Different printing methods, from offset to digital, respond differently to varying speeds. For example, a slow print speed allows for better ink drying and registration, often leading to sharper images and fewer imperfections. Conversely, high speeds can be beneficial for large-volume printing jobs, optimizing throughput. Choosing the appropriate speed is critical for achieving the desired balance between output quality and production time.
Maintaining a consistent printing speed minimizes errors and variations in print quality. Optimizing this parameter improves the reliability of the printing process. Speed control also significantly influences the overall efficiency of the printing operation, impacting production time and cost. This is especially relevant in high-volume commercial printing, where even small increases in speed can translate to substantial savings in time and labor. The selection of speed is often dictated by the type of material being printed, the desired resolution, and the overall volume of the print job. Furthermore, print speed control is crucial for maintaining consistent print quality across different batches, reducing post-printing rework and ensuring customer satisfaction.
- Exploring The Complex Landscape Of Donald Trumps Iq
- Exploring The Life And Achievements Of Oliver Mclanahan Phillips
Pace Printing
Optimizing print speed is vital for maintaining quality and efficiency in various printing processes. Consistent pace printing impacts output quality and production time.
- Speed control
- Ink drying
- Registration accuracy
- Throughput
- Material compatibility
- Resolution adjustment
- Error minimization
- Cost optimization
These key aspects are interconnected. For instance, a slower print speed facilitates better ink drying and registration, preventing smudging and ensuring precise image placement, while faster speeds prioritize higher throughput, beneficial for large-scale productions. Material compatibility is critical; certain papers or inks might require specific speeds to prevent damage or uneven printing. By adjusting resolution, printers can achieve high-quality outputs while maintaining desired print speeds. Error minimization is a direct result of precise control over print parameters like speed, while cost optimization is achieved through balancing speed with quality. These interconnected elements, when managed effectively, lead to a more efficient and controlled printing process.
1. Speed Control
Speed control is a fundamental component of optimized printing, often referred to as "pace printing." Maintaining the appropriate speed throughout the printing process is critical. Varying speeds, or inconsistent pace, can significantly impact the quality and efficiency of the output. A slow pace allows for better ink drying, leading to sharper images and improved registration accuracy. Conversely, rapid speeds, while potentially increasing output volume, can result in smudged prints, misregistration, and a higher rate of errors. Precise speed control is therefore essential for achieving consistent high-quality print jobs across different print runs and volumes.
- Tailormade Udon Delights The Ultimate Guide To Custom Udon
- Best Sivilin Fans Powerful Cooling Solutions
Consider a commercial printing operation. If the printing press operates too rapidly for the chosen ink and paper type, the ink may not dry properly, leading to smudges and defects. This necessitates costly rework and potentially damages the reputation of the printing company. Conversely, if the speed is too low for the printing job's volume, production time increases, making the process less efficient and potentially impacting profitability. Therefore, accurately determining the optimal printing speed is crucial for achieving a balance between quality, speed, and cost-effectiveness. This precise control is directly linked to the overall efficiency and cost-effectiveness of the printing operation. Examples include adjusting printing speeds for different substrates, optimizing ink drying times depending on the type of ink used, and ensuring consistent registration across multiple print runs.
In summary, speed control, a vital element of pace printing, is crucial for maintaining high-quality prints. This control ensures efficient printing procedures by minimizing production time, maximizing output quality, and mitigating errors. Understanding and implementing appropriate speed controls allows for a balanced approach, where print volume, print quality, and production time are all optimized.
2. Ink Drying
Ink drying is a critical component of the printing process, directly intertwined with printing speed. The rate at which ink dries significantly influences the quality and longevity of the printed product. Slower printing speeds often allow for adequate ink drying time, reducing the risk of smudging, feathering, or other print defects. Conversely, high printing speeds may not afford sufficient time for ink to dry properly, leading to these imperfections. This relationship is especially pronounced with certain ink types, substrates, and environmental conditions. A crucial aspect of efficient print production lies in the ability to correctly correlate printing speed with ink characteristics and drying times.
Consider a print run for high-volume marketing materials. If the press operates at a speed that prevents the ink from fully drying, the finished products may exhibit unacceptable imperfections, potentially requiring costly rework or compromising the product's visual appeal. This example highlights the practical significance of accurately assessing the drying characteristics of specific inks and the corresponding printing speeds that prevent issues. Further complications can arise with variable environmental factors. Elevated temperatures or humidity levels can alter ink drying times, necessitating adjustments to the printing process for maintaining quality. Understanding the interplay between print speed, ink properties, and environmental conditions is essential for achieving consistent and high-quality print output. The relationship between ink drying time and print speed is not merely theoretical; it directly translates to quality control and production efficiency.
In conclusion, the connection between ink drying and printing speed is fundamental to high-quality print production. Understanding the dynamics of ink drying, including its relationship with ink type, substrate, and environmental factors, is crucial for achieving optimal print results. Print facilities must carefully calibrate printing speeds to allow adequate drying time to prevent defects. Failure to do so may result in significant operational inefficiencies and increased costs associated with quality control. This knowledge, therefore, underpins the efficient management and control of the printing process, impacting both the final product quality and the overall profitability of the operation.
3. Registration Accuracy
Precise alignment, or registration, of printed elements is paramount for high-quality print products. The speed at which printing occurs directly affects registration accuracy. Maintaining consistent registration across multiple print runs or batches is crucial for achieving a professional finish and avoiding costly rework.
- Impact of Speed on Alignment
High printing speeds can compromise registration accuracy. Moving parts of the printing press, such as plates or rollers, may not have sufficient time to maintain precise alignment at rapid speeds. This can result in misaligned images, text, or other printed elements, impacting the overall aesthetic quality and potentially rendering the final product unusable. Conversely, slower speeds typically improve the precision of registration, enabling more accurate placement of printed elements. This is particularly critical for complex layouts or multi-color prints, where precise alignment is vital for achieving a professional appearance.
- Effects on Substrate and Ink
The properties of the printing substrate (e.g., paper type, thickness) and ink used can also influence the relationship between printing speed and registration. Certain substrates may stretch or warp during the printing process at high speeds, leading to misregistration. Similarly, ink viscosity and drying time can be affected by printing speed, potentially leading to inconsistent registration. Understanding the specific characteristics of the substrate and ink used is critical to optimizing printing speed while maintaining registration accuracy.
- Quality Control and Error Reduction
Careful monitoring and control of printing speed are essential elements of quality control procedures. Slowing down the printing process can help identify and rectify potential misregistration issues earlier in the printing cycle, preventing costly corrections later on. Strict adherence to prescribed printing speeds and regular calibration of printing equipment can minimize errors and maintain consistent registration accuracy across different print runs. Implementing quality checks at various stages of the process is critical to this control system.
- Efficiency and Cost Implications
While slower speeds contribute to accurate registration, excessive slowdowns affect production efficiency and overall printing costs. Finding the ideal balance between printing speed and registration accuracy is crucial for optimal results. Optimizing the printing workflow, including press setup and operator training, is paramount to maintain a steady pace with the required accuracy, resulting in a cost-effective production environment.
In conclusion, maintaining registration accuracy is intricately linked to print speed. Understanding how various factors influence registration, such as substrate properties, ink characteristics, and equipment calibration, is essential for producing high-quality print products. Striking the optimal balance between speed and accuracy is crucial for both quality and efficiency in the printing process. Failure to do so can result in a cascade of issues, affecting not only the aesthetic appeal of the print but also the economic viability of the entire operation.
4. Throughput
Throughput, in the context of printing, represents the volume of output produced over a given period. This measure is intrinsically linked to "pace printing" as efficient processing directly impacts the speed at which products are completed. Maximizing throughput while maintaining quality is a core concern for printing operations, as it affects production efficiency and cost-effectiveness.
- Impact on Production Time
Higher throughput generally translates to faster production cycles. A printing operation achieving high throughput completes orders more quickly, impacting customer satisfaction and revenue generation. Conversely, low throughput extends production times, potentially leading to delays in fulfilling orders and impacting the profitability of the printing business. This relationship highlights the direct correlation between the pace of printing and overall production turnaround.
- Influence on Resource Utilization
Throughput directly correlates with the utilization of printing resources like presses, personnel, and materials. High throughput often suggests optimized resource allocation and efficient workflow processes, whereas low throughput might indicate bottlenecks or inefficiencies within the printing system. This connection underscores the importance of optimizing resource allocation for increased throughput and improved overall operation.
- Effect on Quality Control
Maintaining consistent quality during high-throughput operations is crucial. A press operating at a rapid pace must still maintain high standards in print quality, registration, and color accuracy. Inadequate mechanisms for quality control at high speeds often lead to increased errors and rework, diminishing the benefits of high throughput and ultimately affecting the final product quality. This emphasizes the need for robust quality assurance processes to support the speed of operation.
- Relationship with Capacity and Costs
Throughput is directly related to the printing system's capacity. A system operating beyond its capacity, aiming for extremely high throughput, can lead to quality deterioration and equipment strain. This can lead to increased maintenance costs and downtime. Conversely, operating below capacity results in low throughput and unused potential, reducing overall output and increasing production costs per unit. The optimal throughput is often determined by a careful balancing act between utilizing system capacity efficiently while maintaining print quality.
In summary, throughput is a key performance indicator closely tied to pace printing. Efficient operations strive for high throughput while simultaneously ensuring high-quality outputs. Balancing throughput with quality control measures is essential to maximizing production efficiency and minimizing costs. This balance is crucial for the long-term success and profitability of a printing operation. Furthermore, understanding the interplay between throughput, resource utilization, and quality is paramount for informed decisions related to pace printing and operational improvements.
5. Material Compatibility
Material compatibility in printing plays a critical role in the success of any print job, directly influencing the "pace printing" process. The interaction between the printing material (paper, cardstock, film, etc.) and the printing process parameters, including speed, directly affects print quality and production efficiency. Mismatches can lead to problems ranging from poor image quality to equipment damage, impacting both the speed and the quality of the output.
Consider a commercial print run for high-volume marketing brochures. If the paper stock selected is too thin for the intended printing speed, the paper may stretch or warp, leading to misregistration, smudging, and even equipment damage. This directly impacts the production schedule. Alternatively, a paper stock with poor ink absorption might require a slower printing speed for optimal ink transfer, compromising the throughput of the printing process. Conversely, the correct combination of paper type, ink type, and printing speed allows for optimal print quality at higher production rates. This relationship highlights the importance of material compatibility analysis in optimizing print workflows and preventing costly issues.
In summary, selecting compatible printing materials is crucial for maintaining consistent print quality and optimal printing speeds. This includes understanding the paper's thickness, weight, and absorbency, and how these properties influence ink transfer and drying times. Appropriate material selection allows for higher production speeds without compromising print quality, thereby significantly impacting the efficiency and profitability of printing operations. Ignoring material compatibility can lead to costly rework, delays in production schedules, and potential damage to printing equipment. Therefore, careful consideration of material compatibility is fundamental to efficient and effective "pace printing" strategies.
6. Resolution Adjustment
Resolution adjustment in printing significantly influences the pace of the printing process. Higher resolutions, demanding greater detail, often necessitate slower printing speeds. This is due to the increased data volume requiring processing and transmission. Conversely, lower resolutions, requiring less intricate detail, allow for faster print speeds and higher throughput. The interplay between resolution and printing speed is fundamental to optimizing the efficiency of printing operations.
Practical examples illustrate this relationship clearly. High-resolution images for professional-quality photo prints might necessitate slower speeds to ensure accurate color reproduction and detail retention. Meanwhile, low-resolution images for quick, mass-produced documents can be printed at higher speeds with negligible quality loss. Furthermore, the type of printing technology also impacts the relationship. Digital printing systems may offer more flexibility in adjusting resolution and speed, while offset printing might have constraints impacting this dynamic. The choice of resolution directly impacts the time needed for the entire printing process, from setup to completion. Businesses must carefully balance resolution demands with production timelines and operational costs. A higher resolution may improve the visual appeal of a product, but also prolongs the production time, impacting turnaround time and overall profitability. Conversely, using a lower resolution could compromise print quality and customer satisfaction, despite quicker production.
In conclusion, resolution adjustment is an integral component of "pace printing." Choosing the appropriate resolution directly impacts printing speed, throughput, and overall efficiency. Balancing resolution requirements with operational needs is crucial for optimizing print production and achieving a balance between quality, speed, and cost-effectiveness. A clear understanding of this relationship enables printers to select the optimal resolution for various printing applications, resulting in efficient and cost-optimized processes. This critical understanding enables businesses to accurately assess printing needs and ensure alignment between output quality and production demands. Failing to recognize this link could result in slower production, increased costs, and potential dissatisfaction with print output quality.
7. Error Minimization
Minimizing errors is a critical aspect of any efficient printing operation, directly impacting the overall quality and profitability of the process. The pace at which printing occurs significantly influences error rates. Optimized speed control, often referred to as "pace printing," is directly correlated with reduced errors, enabling a smoother workflow, improved product quality, and minimized post-production corrections.
- Impact of Speed on Error Rates
High printing speeds, while potentially increasing throughput, often correlate with a higher likelihood of errors. Rapid movements of machinery, ink drying inconsistencies, and inadequate time for quality checks increase the probability of misregistration, smudging, ink smears, and other defects. Conversely, slower speeds allow for more accurate registration, better ink drying, and more thorough quality control checks, reducing the incidence of errors.
- Preventive Measures and Quality Control
Implementing robust quality control procedures at various stages of the printing process is fundamental for minimizing errors. Regular calibration of printing equipment, meticulous monitoring of ink characteristics and substrate properties, and stringent adherence to pre-defined printing parameters are crucial preventative measures. Such measures contribute significantly to minimizing errors that could arise due to inconsistencies in speed or other factors during the printing process.
- Role of Operator Expertise
Skilled operators are essential for minimizing errors, particularly in complex printing jobs. Their expertise in recognizing and mitigating potential issues related to speed, ink, and substrate compatibility ensures a smooth and accurate printing process. Training and experience allow operators to identify anomalies early in the printing cycle and adjust accordingly, which significantly reduces error propagation.
- Cost Considerations in Error Reduction
The cost of errors in printing can be substantial. Rework, re-runs, and material waste related to errors represent significant financial losses. Implementing strategies for error minimization, including careful speed control, leads to lower production costs by reducing the need for post-printing corrections. Investing in preventative measures and quality checks translates to savings in the long run.
In conclusion, error minimization is a key component of effective "pace printing." A thorough understanding of the relationship between printing speed and error rates, alongside preventive measures and skilled personnel, is crucial for successful and efficient printing operations. Minimizing errors not only enhances product quality but also significantly impacts the overall cost-effectiveness and efficiency of the entire printing process. This direct relationship underscores the importance of careful control over printing parameters to achieve optimal results.
8. Cost Optimization
Cost optimization in printing is fundamentally linked to the management of printing speed, often referred to as "pace printing." Optimal printing speed directly influences numerous cost factors throughout the production process. Efficient pace printing strategies minimize material waste, reduce labor costs, and minimize the need for costly rework, leading to substantial savings. Inaccurate or inappropriate speed choices can conversely increase production costs. Understanding this crucial relationship is essential for effective cost management within printing operations.
Several factors contribute to the connection. Firstly, faster printing speeds can increase throughput, leading to a higher volume of output in a given time frame. While this potentially reduces per-unit costs, it must be carefully balanced with quality control. Conversely, excessive speed can lead to higher error rates, requiring expensive rework. Secondly, appropriate material selection and ink usage are heavily dependent on the printing speed. Using the wrong paper for a specific speed, for instance, could cause damage to the printing machinery or result in a poor print quality requiring rework. Thirdly, skilled labor, effectively utilized with proper pace, significantly impacts efficiency. Inadequate control over speed can lead to inefficient use of skilled labor, increasing operational costs. The most cost-effective approach often involves identifying the optimal printing speed for a specific job, balancing speed with quality and minimizing material waste.
The practical significance of this understanding is substantial. A print shop not optimizing printing speed can experience significant financial losses from wasted materials, increased rework, and reduced overall efficiency. Knowing the optimal speed for particular substrates, inks, and print jobs allows print shops to reduce material costs. Optimized speed control also allows businesses to effectively utilize labor, reducing labor costs and improving turnaround times. By meticulously managing printing pace, operations can achieve significant cost savings without compromising print quality. Ultimately, cost optimization through "pace printing" translates to greater competitiveness in a market driven by efficiency and cost-effectiveness. A concrete example is an offset printing operation choosing the optimal speed for a specific paper stock, thereby minimizing paper waste and maximizing print quality, resulting in substantial cost savings.
Frequently Asked Questions about Pace Printing
This section addresses common questions about "pace printing," a critical aspect of print production. Understanding these concepts is essential for achieving optimal print quality and efficiency.
Question 1: What is pace printing, and why is it important?
Pace printing refers to the strategic adjustment of printing speed to optimize the printing process. Maintaining the appropriate speed is critical for several reasons. First, it directly impacts print quality. Different substrates and inks require specific drying times. Incorrect speeds can lead to smudging, misregistration, or other defects. Second, proper pace optimization improves overall efficiency, reducing material waste and rework. Finally, optimal printing speed contributes to lower production costs and faster turnaround times.
Question 2: How does printing speed affect print quality?
Printing speed significantly impacts print quality. Higher speeds often lead to decreased print quality due to insufficient ink drying time, causing problems like smudging or uneven color distribution. Conversely, excessively slow speeds can cause issues like paper stretching or warping, affecting registration and final output. Finding the optimal balance is crucial.
Question 3: What factors influence the ideal printing speed?
Several factors determine the ideal printing speed. The type of ink, paper stock, and printing method are crucial considerations. Environmental conditions, like humidity and temperature, can also influence ink drying times and thus required speeds. Furthermore, the complexity of the print job and the desired resolution impact the appropriate pace. Printing presses and specific equipment limitations should also be considered.
Question 4: How can businesses optimize pace printing for cost savings?
Optimizing pace printing for cost savings requires careful analysis and planning. The primary goal is finding the right balance between speed and quality to minimize material waste and rework. Employing a thorough understanding of equipment limitations and optimal speeds for particular substrates and inks is key. Implementing consistent quality control procedures throughout the printing process and training staff to recognize and avoid potential errors further contribute to cost savings.
Question 5: What are the potential consequences of ignoring pace printing principles?
Ignoring pace printing principles can lead to significant issues, ranging from poor print quality and increased rework to damaged equipment and production delays. Inconsistent print quality can harm the business's reputation and lead to customer dissatisfaction. Material waste, extended production times, and increased labor costs are other potential consequences.
In summary, understanding the interplay between printing speed, material characteristics, and environmental factors is vital for any printing operation. Proper optimization, often referred to as pace printing, directly impacts print quality, efficiency, and cost-effectiveness. By carefully managing these variables, businesses can achieve optimal results.
Next, we will explore specific methodologies and technologies utilized in contemporary printing operations.
Conclusion
This article has explored the multifaceted role of "pace printing" in contemporary print production. Key findings emphasize the crucial link between printing speed and various aspects of the process, including print quality, efficiency, and cost-effectiveness. The analysis demonstrated that maintaining an optimal printing pace is essential for high-quality output, minimizing material waste, and maximizing throughput. Factors such as ink drying time, substrate characteristics, and equipment limitations were identified as critical considerations in establishing an appropriate printing rhythm. Further, the article highlighted the importance of skilled labor and quality control in maintaining consistent output at varying production paces. A thorough understanding of these interconnected elements is vital for effective cost management and successful print operations.
The future of print production hinges on continued refinement of pace printing strategies. Integration of advanced technologies and data-driven approaches can enhance decision-making regarding optimal printing speeds, thereby optimizing resource utilization and minimizing operational costs. Precision control over print parameters, including speed, resolution, and registration, is essential to meet evolving market demands for both high-quality output and quick turnaround times. Moreover, proactive investment in training and maintenance of printing equipment is crucial for consistent, efficient, and high-quality print output across varying production volumes. Ultimately, mastery of pace printing principles will be instrumental in ensuring the continued relevance and competitiveness of print production in the face of digital advancements.
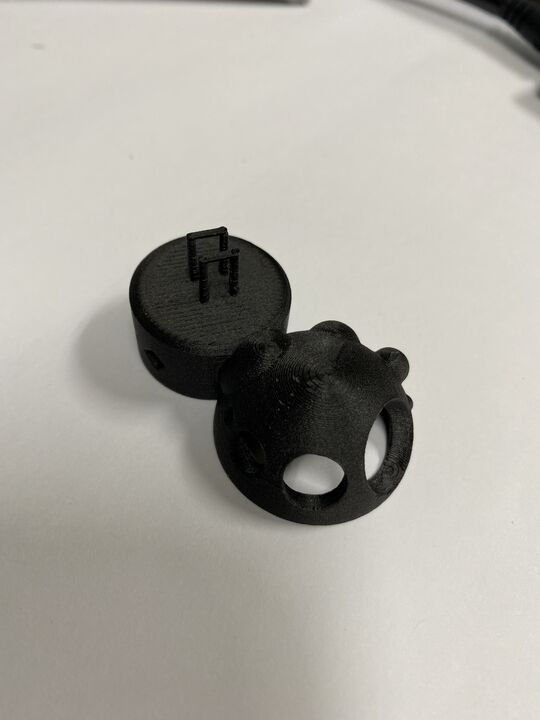
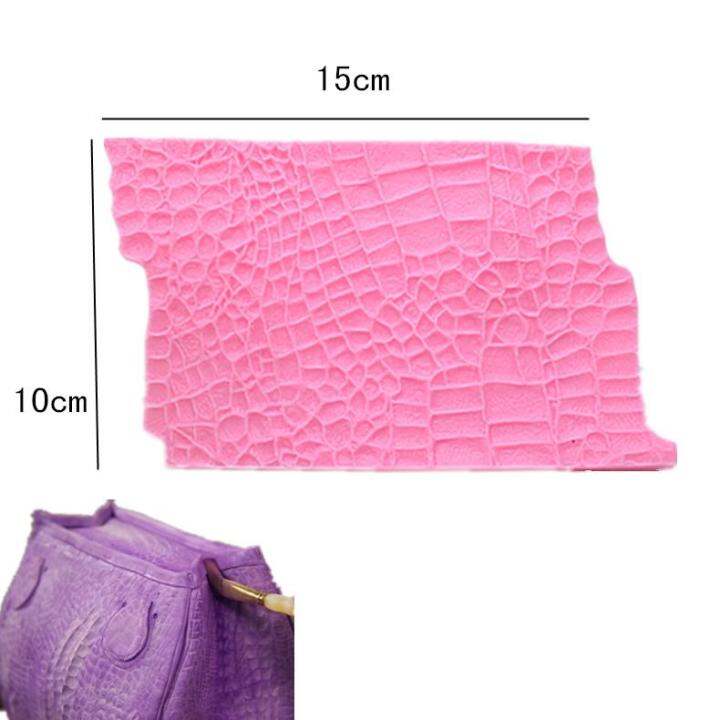
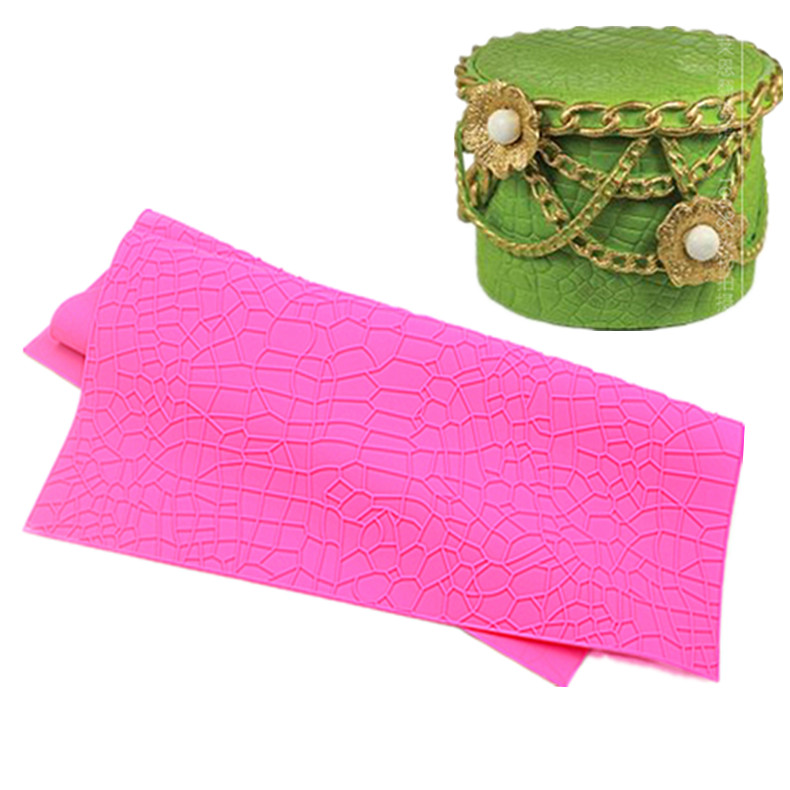
Detail Author:
- Name : Ansley McClure DDS
- Username : fboehm
- Email : hherzog@torphy.com
- Birthdate : 1970-03-22
- Address : 9457 Ed Junction Lake Tristonmouth, TN 02869-9389
- Phone : +1 (719) 731-2250
- Company : Gibson-Will
- Job : Animal Trainer
- Bio : Voluptatem magnam alias distinctio reprehenderit aliquid totam fugiat illo. Suscipit consequatur culpa cumque odit totam rerum.
Socials
facebook:
- url : https://facebook.com/volkman2013
- username : volkman2013
- bio : Incidunt dignissimos velit minus iste quibusdam dignissimos accusamus quis.
- followers : 2336
- following : 2134
tiktok:
- url : https://tiktok.com/@avolkman
- username : avolkman
- bio : Maiores aut accusantium aliquid. Rem earum quasi aliquam qui fuga.
- followers : 2138
- following : 1687