Best Tileco Flooring Options & Deals Now!
What is this specialized system for managing and optimizing building materials? A system for efficient material management in construction is crucial.
This system, often employed in modern construction projects, involves a comprehensive approach to managing building materials. It encompasses inventory control, procurement, tracking, and distribution. For instance, a project might utilize software to maintain precise records of all tiles, bricks, or other construction materials. This ensures proper quantities are available at each stage of the building process, avoiding delays and cost overruns. The system helps streamline the entire supply chain.
Such a system offers significant advantages in terms of cost control and project efficiency. By precisely monitoring material usage, potential waste is minimized, leading to savings. This also helps in meeting project deadlines more reliably by ensuring materials are available when and where needed. The historical context reveals an increasing emphasis on optimized project management, and this system serves as a significant tool in that evolution. Furthermore, it facilitates better communication and collaboration between project stakeholders.
Moving forward, this discussion will examine specific examples of how such a system can be implemented in different building types and scales, along with its impact on the overall construction industry.
Tileco
Understanding the essential components of a comprehensive tile management system is crucial for effective construction projects. Such a system, encompassing various aspects, optimizes material usage, reduces waste, and streamlines project timelines.
- Inventory Tracking
- Procurement Management
- Distribution Optimization
- Cost Control
- Waste Minimization
- Project Efficiency
These key aspects of a comprehensive tile management system are interconnected. Precise inventory tracking enables informed procurement decisions, reducing material waste. Optimized distribution ensures timely delivery to the project site, enhancing project efficiency. Effective cost control, through the analysis of material usage, further minimizes project overruns. Ultimately, these elements contribute to a comprehensive system that bolsters project success, by minimizing waste, and optimizing project workflow. For example, a well-managed system can accurately track how many tiles are needed, leading to an appropriate amount of tiles being purchased and reducing excess materials. This reduces costs and minimizes waste, thereby increasing efficiency and profits.
1. Inventory Tracking
Accurate inventory tracking is a fundamental component of a comprehensive material management system. In the context of managing construction materials, precise tracking of tilesand other building materialsdirectly impacts project success. Without robust inventory tracking, construction projects risk significant material shortages, leading to delays and escalating costs. Conversely, effective tracking ensures materials are available when needed, minimizing disruptions and preventing costly project overruns. This applies to all types of construction projects, from small residential renovations to large commercial developments.
A well-designed inventory system for tiles allows for real-time visibility into material levels. This visibility facilitates proactive procurement decisions, preventing stockouts and ensuring materials are available at each stage of the construction process. For example, if a project anticipates a surge in tile demand during a particular week, an accurate inventory tracking system enables timely ordering and prevents a critical shortage that would delay the project and increase costs. Furthermore, tracking allows for the identification of slow-moving inventory, potentially enabling adjustments to procurement strategies and minimizing the accumulation of unused materials.
Effective inventory tracking within a material management system is crucial for project profitability and efficiency. Accurate data on tile quantities, locations, and conditions facilitates streamlined project workflows. Understanding the direct correlation between meticulous inventory tracking and cost control is vital. By minimizing material waste and ensuring timely availability, robust inventory tracking directly contributes to the overall success of construction projects. In conclusion, robust inventory tracking is not merely a bookkeeping function but a cornerstone of effective material management in any construction project.
2. Procurement Management
Effective procurement management is intrinsically linked to the success of any construction project, particularly when dealing with specialized materials like tiles. Procurement encompasses the entire process of acquiring the necessary materials, from initial sourcing to final delivery. Within the context of "tileco," or a comprehensive tile management system, this process becomes even more critical, dictating the availability, quality, and cost of tiles for the project.
- Supplier Selection and Negotiation
Identifying reliable suppliers of high-quality tiles is paramount. This involves researching various suppliers, evaluating their capabilities, and negotiating favorable pricing and delivery terms. For instance, a project might compare pricing and lead times from different tile manufacturers or distributors to ensure optimal value. The selection process directly impacts the overall cost and availability of tiles within the system.
- Order Placement and Tracking
Accurate and efficient order placement is crucial. Integration with the tileco system enables automated order processing, reducing the potential for errors and delays. Effective tracking allows for real-time monitoring of order status, preventing unexpected delays and ensuring timely delivery to the project site. This efficiency is vital for maintaining project schedules.
- Quality Control and Inspection
Implementing robust quality control procedures is essential to ensure the purchased tiles meet project specifications. This involves inspecting incoming shipments for defects, verifying compliance with standards, and rejecting any substandard materials. Integration with a tileco system allows for efficient recording and tracking of quality assurance measures, reducing the risk of incorporating faulty tiles and preventing costly rework or project delays. Detailed documentation of these inspections is paramount for proper project management and dispute resolution.
- Inventory Management Integration
Effective procurement management seamlessly integrates with the overall inventory management within the tileco system. Accurate order forecasting, based on project needs and existing inventory, is critical for minimizing waste and maximizing material utilization. This integration avoids overstocking and ensures tiles are available when required. The system tracks real-time inventory levels to proactively adjust procurement decisions, preventing material shortages and delays.
In conclusion, robust procurement management directly contributes to the effectiveness of a "tileco" system. By streamlining the acquisition process, ensuring quality, and integrating with the overall inventory management, procurement management plays a pivotal role in optimizing material flow and ensuring project success. A well-coordinated procurement process supports project timelines, budget adherence, and final product quality.
3. Distribution Optimization
Distribution optimization within a comprehensive material management system, exemplified by "tileco," is crucial for the successful execution of construction projects. Optimized distribution directly impacts project timelines, costs, and overall efficiency. Efficient movement of tiles and other construction materials from the point of procurement to the construction site ensures availability when needed, minimizing delays and rework.
- Route Planning and Logistics
Strategic route planning and logistics management minimize transportation time and costs. Sophisticated software integrated with a tileco system can analyze various delivery routes, considering factors like traffic patterns, delivery windows, and geographic constraints to establish the most efficient pathways. This optimizes transit time and reduces fuel consumption, contributing to environmentally sustainable practices. Furthermore, effective logistics minimizes the risk of material damage during transit. For instance, a system might route deliveries to different project phases to minimize unnecessary travel, reducing wear and tear on the delivery vehicles.
- Inventory Management Integration
Distribution optimization is inextricably linked to inventory management. Real-time tracking of tile and material locations through the "tileco" system enables precise delivery scheduling. The system can predict material demands at different project phases, facilitating proactive delivery scheduling. This minimizes the risk of material shortages at crucial project stages. Data analysis informs delivery schedules, preventing stockouts and ensuring that materials are available as needed, supporting on-schedule project completion.
- Warehouse Management and Storage
Efficient warehouse management is crucial for effective distribution. A tileco system could optimize storage space by strategically arranging materials to maximize accessibility and minimize movement. Tracking inventory within the warehouse ensures efficient retrieval of materials. This contributes to a highly organized workspace and enables quick material access for various project phases. Further, the system can identify and address storage concerns, including issues with material damage or degradation, ultimately impacting material quality throughout the construction process.
- Delivery Scheduling and Control
Optimized delivery scheduling integrates with the overall project timeline, ensuring materials are delivered on time. By synchronizing delivery schedules with the construction schedule, project delays due to material shortages are minimized. The system can facilitate communication with delivery drivers, construction personnel, and other stakeholders to refine delivery schedules in real time, addressing unforeseen issues and delays. In essence, a centralized system, such as a "tileco" system, provides a comprehensive view of delivery progress and enables agile adjustments throughout the project lifecycle.
Ultimately, distribution optimization, as integrated into a "tileco" system, encompasses a proactive approach to material movement. By strategically planning routes, integrating with inventory, optimizing storage, and effectively controlling deliveries, the system creates a highly responsive and efficient material supply chain. This streamlined process contributes directly to project profitability and ensures material availability throughout the construction cycle, minimizing disruptions and enhancing the overall success rate.
4. Cost Control
Effective cost control is a critical component of any comprehensive material management system, particularly in construction. A system like "tileco," designed for managing tiles and other building materials, directly benefits from precise cost control mechanisms. Accurate tracking of material costs, from initial procurement to final installation, is essential for preventing project overruns and maximizing profitability. Real-world examples demonstrate how inadequate cost control can lead to substantial financial losses. A project exceeding its budget due to unforeseen material costs can significantly impact profitability and project timelines.
The integration of cost control within a "tileco" system facilitates several key advantages. Precise records of tile acquisition costs, including transportation, handling, and storage, allow for accurate project budgeting. This allows for the identification of potential cost variances early in the project, enabling proactive adjustments. Detailed tracking of material usage further refines cost estimates, providing a more accurate representation of the overall project budget. Analyzing historical data on material costs assists in forecasting future expenditure and in making informed procurement decisions. This proactive approach minimizes the risk of cost overruns and supports the successful completion of the project within the defined budget. For example, a "tileco" system that tracks tile usage in real-time might identify that a particular tile type is being consumed at a significantly higher rate than anticipated. This early identification allows project managers to explore alternative, more cost-effective options before the cost difference becomes substantial.
In conclusion, effective cost control is not just a component of a "tileco" system but rather an integral part of its functionality. By incorporating accurate cost tracking, comprehensive budgeting, and variance analysis, such a system empowers project managers to make data-driven decisions. This allows for proactive adjustments and helps ensure projects are completed within budget and schedule, contributing significantly to overall project profitability. Understanding the interconnectedness between cost control and material management systems like "tileco" is essential for optimizing construction projects and minimizing financial risks.
5. Waste Minimization
Waste minimization is a critical element within a comprehensive material management system like "tileco." Effective tile management directly impacts waste generation. Precise inventory tracking, detailed procurement procedures, and optimized distribution strategies all contribute to minimizing material waste. Reduced waste translates to lower material costs and reduced environmental impact. A significant portion of construction waste arises from excessive material procurement, poor inventory control, or inaccurate project estimations.
Accurate inventory tracking, a core function of "tileco," allows for proactive management of material levels. By closely monitoring available quantities, unnecessary purchases are avoided. Detailed procurement processes, encompassing precise order placement and quality control, ensure only the necessary materials are acquired, minimizing surplus. Optimized distribution strategies, which integrate with real-time inventory updates, optimize delivery routes and minimize material handling, thus lowering the risk of damage during transport and reducing the volume of discarded materials. These factors work in tandem, effectively reducing construction waste at every stage of a project. For example, if a project correctly forecasts tile needs and orders materials only as required, less tile is left over after completion of the project, leading to significantly lower waste levels.
Understanding the connection between waste minimization and "tileco" is vital for sustainable construction practices. Reduced waste contributes to lower project costs, improved efficiency, and a more sustainable environmental footprint. Moreover, minimizing construction waste positively impacts the bottom line. The successful implementation of effective material management strategies within a project reduces the risk of material spoilage, damage, or obsolescence, thereby enhancing profitability. By incorporating waste minimization into the core framework of "tileco," construction projects can attain significant cost savings and positive environmental outcomes. Ultimately, the implementation of such strategies, like those embedded within "tileco," contributes to a more eco-conscious and cost-effective approach to building. This understanding is vital for promoting environmentally responsible and financially astute construction practices.
6. Project Efficiency
Project efficiency is paramount in construction, and a robust system for managing materials like "tileco" directly impacts this metric. A well-orchestrated material management system reduces project delays and enhances overall productivity. This stems from the ability to anticipate material needs, ensure timely delivery, and minimize rework due to material shortages or discrepancies. By streamlining the procurement, storage, and distribution of tiles, a system like "tileco" contributes significantly to the efficiency of the entire project lifecycle.
Real-world examples illustrate the impact of efficient material management. Projects plagued by material shortages experience delays and cost overruns. Conversely, projects with meticulous material control, leveraging a system like "tileco," often meet deadlines more reliably and operate within budget. Accurate inventory tracking within "tileco" provides real-time visibility into material levels. This, in turn, facilitates precise ordering and minimizes the risk of critical material shortages that can halt construction activities. Such proactive management translates directly into increased project efficiency. The effective scheduling of material deliveries, enabled by the integrated logistical capabilities of "tileco," further reduces project delays. Moreover, minimizing material waste, another outcome of "tileco," avoids costly rework and reordering, thereby maintaining project momentum and budget adherence.
In conclusion, a well-structured material management system, epitomized by "tileco," plays a vital role in achieving project efficiency. By streamlining material handling, optimizing logistical aspects, and minimizing disruptions, "tileco" empowers projects to remain on schedule, within budget, and with fewer rework incidents. This direct correlation between material management systems and overall project performance highlights the crucial importance of adopting effective approaches to optimize construction processes. Further research into and implementation of advanced material management systems, like "tileco," hold significant potential for further enhancing project efficiency and reducing construction project vulnerabilities.
Frequently Asked Questions about Tileco
This section addresses common inquiries regarding Tileco, a comprehensive material management system for construction projects. These questions and answers provide valuable insights into the system's functionality and benefits.
Question 1: What is Tileco, and how does it differ from traditional material management methods?
Tileco represents a modern, integrated approach to managing construction materials, particularly tiles. Unlike traditional methods, which often rely on disparate systems for inventory, procurement, and distribution, Tileco consolidates these functions into a unified platform. This integration streamlines workflows, minimizes errors, and enhances visibility across the entire material lifecycle, leading to greater efficiency and cost savings.
Question 2: What are the key benefits of implementing Tileco?
Key benefits of Tileco include improved cost control through precise inventory management and minimized material waste. Enhanced project efficiency results from proactive material procurement and optimized distribution. Accurate tracking and reporting provide stakeholders with real-time visibility into project status and material availability. Reduced risk of delays and project overruns due to material shortages is another significant advantage.
Question 3: How does Tileco improve inventory management?
Tileco utilizes advanced software to track inventory levels in real-time. This includes precise location tracking, allowing for streamlined retrieval and optimized storage space utilization. The system also incorporates automated ordering processes, reducing the risk of stockouts and ensuring materials are available when needed. Comprehensive data analysis aids in predicting future material requirements, further optimizing inventory management.
Question 4: Does Tileco integrate with other project management software?
Tileco is designed for seamless integration with existing project management software platforms. This interconnectedness allows for a holistic view of project data, facilitating better coordination and communication amongst project stakeholders. Integration ensures data consistency and minimizes the risk of information silos within the project.
Question 5: How can Tileco contribute to a sustainable construction approach?
Tileco's efficiency in material management contributes significantly to sustainable construction practices. By reducing waste, minimizing material shortages, and optimizing resource allocation, the system minimizes the environmental impact of construction projects. This approach reflects a commitment to responsible resource utilization and minimizes the negative impact on the environment.
Understanding these key aspects of Tileco helps stakeholders appreciate its value in modern construction projects.
Moving forward, this document will delve deeper into the specific modules and functionalities within the Tileco system.
Conclusion
This exploration of "tileco," a comprehensive material management system, highlights its multifaceted benefits in modern construction projects. Key aspects discussed include the crucial role of precise inventory tracking in optimizing procurement decisions and minimizing waste. Effective procurement management, encompassing supplier selection and quality control, ensures timely delivery of high-quality materials. Optimized distribution strategies, integrating with real-time inventory updates, minimize logistical challenges and enhance project efficiency. Cost control, facilitated by meticulous tracking of material usage and expenditures, enables better budget management and project profitability. Further, "tileco" promotes a sustainable approach by reducing waste generation and optimizing resource utilization. Ultimately, "tileco" offers a comprehensive solution to streamline material management, leading to more efficient, cost-effective, and sustainable construction projects.
In conclusion, the adoption of "tileco" systems is crucial for contemporary construction. Their impact extends beyond mere material management, influencing project timelines, cost effectiveness, and overall sustainability. Future advancements in "tileco" technology will likely involve enhanced integration with other project management software, predictive analytics for improved material forecasting, and further optimization of supply chain logistics. The implications for the construction industry are substantial, emphasizing the need for professionals to embrace these systems for competitive advantage and long-term project success. Continuous development and adaptation of "tileco" systems will be vital to meet the evolving needs of complex and demanding construction projects.

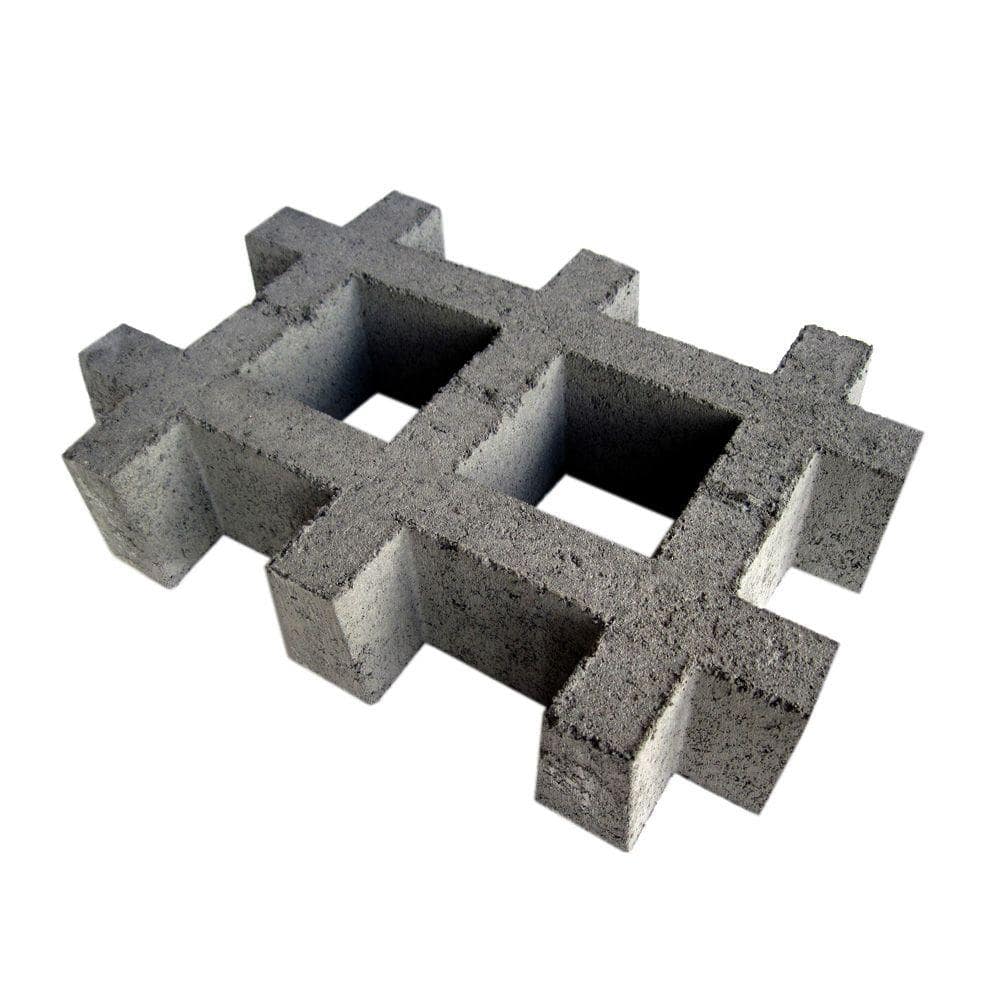
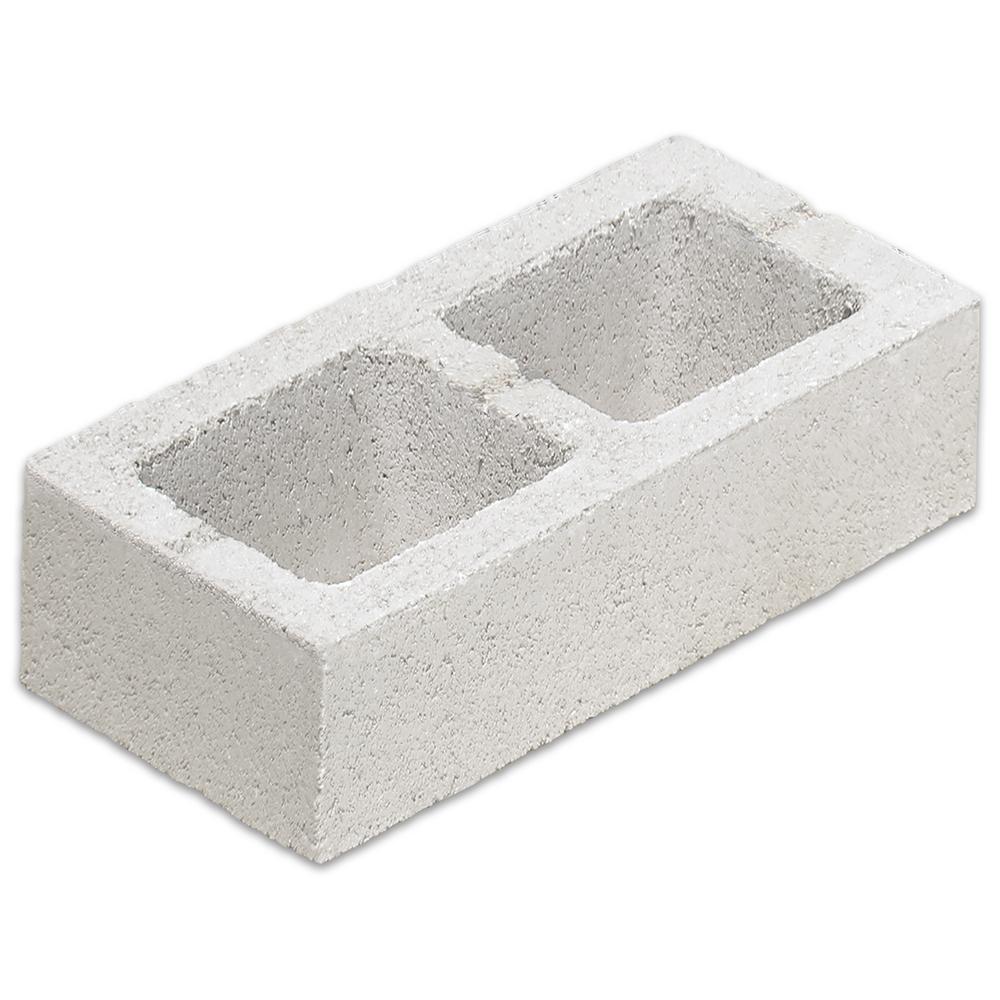
Detail Author:
- Name : Esmeralda Pfannerstill
- Username : elwin38
- Email : prempel@bode.info
- Birthdate : 1981-03-09
- Address : 6079 Greenholt Corner Ellismouth, CO 81927
- Phone : (419) 858-5382
- Company : Kemmer-Eichmann
- Job : Paralegal
- Bio : Provident qui iure saepe autem iste quo. At qui provident animi consequuntur quis sunt repellendus. Asperiores pariatur eius quod aliquid et iste magni.
Socials
linkedin:
- url : https://linkedin.com/in/rosalia_id
- username : rosalia_id
- bio : Consequatur ut atque dolores aut laboriosam.
- followers : 3768
- following : 1851
twitter:
- url : https://twitter.com/hower
- username : hower
- bio : Placeat eum quisquam enim maiores ex. Repudiandae omnis odio velit ea. Quas et vel qui voluptas veniam incidunt.
- followers : 5871
- following : 1029
tiktok:
- url : https://tiktok.com/@rosalia_real
- username : rosalia_real
- bio : Ut architecto aut et eos distinctio est itaque.
- followers : 3703
- following : 1774
facebook:
- url : https://facebook.com/rosalia_howe
- username : rosalia_howe
- bio : Et quia officiis vel odio magnam. Et officiis illo in et quod.
- followers : 5474
- following : 586
instagram:
- url : https://instagram.com/rosaliahowe
- username : rosaliahowe
- bio : Porro consequatur consequatur rem dolorem. Molestiae laudantium facere et possimus.
- followers : 4366
- following : 778