Unveiling Deep Hot Secrets
What are the underlying principles and practical applications of a highly specialized thermal processing technique?
This advanced thermal treatment method involves precise control of temperature and time to achieve specific material alterations. It's characterized by a combination of high temperature and sustained exposure, resulting in significant changes in the physical and sometimes chemical properties of the material. This could include enhanced strength, altered conductivity, or improved resistance to environmental factors. Examples span a wide range from metallurgical processes used in manufacturing to specialized food preservation techniques.
The importance of such specialized thermal treatments lies in their ability to fundamentally alter materials, leading to enhanced performance, durability, and safety. This methodology enables the creation of materials with specific and precisely controlled properties, which are indispensable in numerous fields, from aerospace and engineering to food science and medical technology. Historically, the evolution of understanding heat treatment has led to groundbreaking discoveries and innovations in various industries.
This discussion serves as a foundational introduction to explore the intricacies of this particular thermal treatment technique and its broad application across various disciplines.
Deep Heat Treatment
Understanding deep heat treatment requires examining its core elements. These elements dictate the process's efficacy and application.
- Temperature Control
- Time Duration
- Material Properties
- Process Design
- Equipment Calibration
- Quality Assurance
Temperature control is critical; precise temperature profiles drive the desired structural changes. Time duration, in conjunction with temperature, is crucial, impacting the depth and uniformity of transformation. Material properties influence the treatment's effectiveness and necessary parameters. Process design ensures optimized conditions and predictable outcomes. Equipment calibration is essential to maintain accurate temperature profiles. Finally, quality assurance protocols ensure consistent and reliable results. For instance, meticulously controlled heating cycles in a furnace with calibrated temperature sensors allow for reproducible outcomes, producing materials suitable for various applications, like specialized alloys for aerospace components. These intricate connections between the key aspects demonstrate the complexity and importance of deep heat treatment in modern materials science.
1. Temperature Control
Precise temperature control is fundamental to the efficacy of deep heat treatment processes. Maintaining precise temperature profiles during these treatments is critical for achieving the desired material alterations and ensuring consistent results. Variations in temperature can lead to undesired outcomes, impacting material properties, potentially compromising structural integrity, and rendering the process ineffective or even harmful.
- Gradients and Profiles
Deep heat treatment often necessitates the creation and maintenance of specific temperature gradients within the material. This involves careful design of heating and cooling cycles, ensuring uniform heating throughout the component or part. Uniformity is critical to prevent localized stresses and ensure the desired transformation occurs consistently. For example, in heat treating steel alloys, specific temperature gradients can produce desired hardness distributions, influencing the material's strength and resistance to wear.
- Rate of Heating and Cooling
The rate at which material is heated and cooled significantly influences the final microstructure and resultant properties. Rapid heating and cooling, known as quenching, can lead to different outcomes compared to slower, more controlled heating and cooling cycles. Variations in the heating and cooling rates can result in different metallurgical phases, affecting material properties like hardness, ductility, and resilience. Controlling these rates ensures consistency in the final product and avoids undesirable phase transformations.
- Instrumentation and Calibration
Accurate measurement and control of temperature throughout the process is essential. Sophisticated instrumentation, like thermocouples and temperature sensors embedded in or adjacent to the material, allows real-time monitoring and ensures the process maintains the desired profile. Calibration of this equipment is crucial to avoid errors and maintain accuracy over time. Inaccurate temperature control directly translates into material properties far from design specifications.
- Material-Specific Requirements
Different materials exhibit varying responses to temperature changes. The selection of appropriate heating and cooling protocols must consider the specific material's characteristics. This includes thermal conductivity, phase transformations, and other relevant material properties, ensuring the treatment does not introduce harmful or unpredictable changes. For example, different steel types require distinct heating and cooling schedules for optimal results.
Effective deep heat treatment hinges on precise temperature control. These facets, from gradients and rate control to instrumentation and material considerations, ensure the process produces the desired outcomes, contributing to the reliability and performance of the finished product in applications ranging from structural components to high-performance machinery.
2. Time Duration
Time duration is an integral component of deep heat treatment processes, directly influencing the effectiveness and outcomes. Prolonged exposure to high temperatures, carefully controlled, is often necessary to achieve the desired structural alterations. The duration impacts the depth and uniformity of the transformation. Insufficient time may result in incomplete alteration, while excessive time can cause unwanted degradation or distortion of the material. The relationship between time and temperature during heat treatment is not linear and requires meticulous consideration to optimize material properties.
Real-world examples highlight the crucial role of time duration. In steel metallurgy, a specific annealing process requires a precise heating time to relieve internal stresses and achieve the desired ductility. Similarly, in semiconductor manufacturing, precise time durations for diffusions allow for controlled doping profiles. In food preservation, controlled heating times in retort processes ensure safe and prolonged shelf life. All these examples demonstrate the importance of meticulously calibrated time parameters in achieving the desired effects in deep heat treatments. The optimal time depends intricately on the material's properties, desired characteristics, and the equipment used in the process. Variation in time can lead to significant changes in the final material structure and its properties, ultimately impacting the performance, reliability, and safety of the end product. For instance, excessive time at high temperatures may lead to undesirable grain growth in metals, reducing their strength.
Understanding the relationship between time and temperature in deep heat treatment is vital for achieving consistent and predictable results. It's a foundational principle in various industries, ensuring material quality, longevity, and safety. Optimizing time duration enables consistent material properties, leading to predictable performance in diverse applications, from high-performance machinery to the everyday products we use. The careful manipulation of time during deep heat treatment remains a central aspect of materials science and engineering across numerous fields.
3. Material Properties
Material properties are inextricably linked to the efficacy and outcomes of deep heat treatment. The nature of a materialits composition, structure, and inherent characteristicsdictates the appropriate parameters for deep heat treatment. The selection of suitable processes hinges on these characteristics. Consider the following crucial aspects:
The material's thermal conductivity influences the rate at which heat penetrates the material. Materials with high thermal conductivity necessitate faster heating and cooling rates compared to those with low conductivity. This factor determines the rate of temperature change, directly impacting the resultant microstructure and consequently affecting the material's mechanical properties. For instance, aluminum alloys, known for their high thermal conductivity, require different heating and cooling profiles than stainless steel. Metals with high thermal conductivity, like copper, allow for faster heat transfer, enabling more rapid heating and cooling cycles, facilitating deeper penetrations of heat treatment, while materials with lower conductivity may require more time for uniform heating and cooling. This understanding is essential for achieving the desired properties and avoiding unwanted distortions or material damage.
Chemical composition significantly impacts the transformation temperatures and phases during deep heat treatment. Different elemental constituents react differently to heat, influencing the formation of specific microstructures. Understanding these reactions is vital for controlling the final properties of the material. For instance, the addition of alloying elements to steel dramatically affects its transformation temperatures and mechanical properties during heat treatment, allowing the development of steels with precisely controlled strength, hardness, and ductility. Specific compositional features, like carbon content in steel, dictate the optimal heat treatment procedures. This deep understanding of composition is fundamental for producing materials with tailored performance characteristics.
The initial microstructure of the material profoundly affects its response to deep heat treatment. Existing grain size, crystal orientation, and defect concentration will all influence how the material reacts to the heat application and subsequent cooling. This relationship is especially important in processes where grain refinement or recrystallization is the objective. For example, a material with coarse grains may exhibit reduced strength compared to a material with fine grains, post-deep heat treatment. The initial state of the material forms a critical starting point for the deep heat treatment process, demanding in-depth understanding and meticulous control throughout. This intricate connection between material properties and deep heat treatment underscores the critical need for careful material selection and comprehensive process optimization.
4. Process Design
Process design, a crucial element in deep heat treatment, encompasses the meticulous planning and execution of the thermal process. It entails defining the precise parameters temperature profiles, heating and cooling rates, time durations, and material positioning within the processing apparatus to achieve the desired structural and compositional modifications within the material. Effective process design ensures consistency and repeatability, guaranteeing a predictable outcome, which is paramount for industrial applications. This design process is not simply an afterthought but a cornerstone of the deep heat treatment process, requiring careful consideration of various factors to optimize the final product.
Real-world examples of sophisticated process design in deep heat treatment are abundant. In aerospace industries, precise heat treatments are crucial to achieve the optimal combination of strength and weight in metallic components. The design must account for the specific material composition, intended application, and dimensional tolerances of each part. Similarly, in semiconductor manufacturing, controlled thermal cycles are essential for dopant diffusion and crystal structure refinement. The process design must precisely manage temperature gradients to avoid damage and maintain uniform doping throughout the material. This illustrates that well-defined process designs are essential for achieving the desired material characteristics in different industrial sectors. The intricacy of process design in deep heat treatment demonstrates the precision required for the success of this type of thermal processing.
The significance of process design in deep heat treatment cannot be overstated. It ensures consistency, reliability, and repeatability in producing high-quality material transformations. This approach allows for the standardization of procedures, leading to improved efficiency and reduced waste. Process design is critical not only for producing high-quality components but also for meeting stringent quality control and safety standards. Without robust process design, achieving the desired outcome in deep heat treatment and obtaining materials with tailored properties becomes an exercise in chance rather than controlled method. Understanding and implementing effective process design is thus paramount for modern manufacturing and various applications, ensuring consistency, reliability, and the production of desired materials. The implications extend to the overall economic feasibility and reliability of industrial processes that utilize deep heat treatment.
5. Equipment Calibration
Accurate equipment calibration is indispensable in deep heat treatment processes. Precise temperature control is fundamental to achieving desired material transformations. Calibration ensures accurate measurement and control of temperatures during heating and cooling cycles. Deviations from calibrated readings can lead to inaccurate temperature profiles, resulting in undesirable microstructures, compromised material properties, and ultimately, defective components. Consistent calibration ensures the reliability and repeatability of the process, a cornerstone of quality control.
Consider a scenario in a steel forging facility. Variations in furnace temperature readings, stemming from inaccurate calibration, can lead to inconsistent hardness and strength in the final forged parts. This can manifest as brittle components prone to fracture, or excessively soft parts susceptible to deformation under load. In semiconductor manufacturing, precise thermal cycles are critical for doping and crystal growth. Inaccurate temperature control, arising from faulty calibration of the heating and cooling equipment, can lead to non-uniform doping profiles and flawed semiconductor wafers. Inadequate calibration can impact the yield of usable products and increase production costs due to rework or scrap. Similarly, in food processing applications, accurate calibration of retort equipment is paramount for safety and preservation. Inaccurate temperature readings can result in insufficient sterilization, leading to potential health risks from contamination or inadequate preservation, rendering products unusable.
In conclusion, proper equipment calibration is not a peripheral consideration but rather an essential component of deep heat treatment processes. Maintaining the accuracy of measuring instruments ensures the reliability and consistency of results. Consistent calibration prevents defects in the treated material, ensuring the quality and safety of the end product. The consequences of neglecting calibration extend beyond simply inconsistent outcomes; they can lead to substantial production issues, safety concerns, and ultimately, economic losses. Thus, diligent equipment calibration is crucial for the effective and safe application of deep heat treatment procedures across diverse industrial sectors.
6. Quality Assurance
Quality assurance (QA) is integral to deep heat treatment processes. Maintaining consistent and predictable outcomes is paramount. QA procedures ensure the integrity and reliability of the heat-treated material, verifying that the process meets predetermined standards and specifications. Defects in the heat treatment process can lead to material failure, safety issues, and economic losses. Robust QA protocols are therefore critical for minimizing these risks.
- Monitoring and Measurement
Continuous monitoring of critical parameters during heat treatment is fundamental. This includes real-time tracking of temperature, time, and atmosphere conditions within the processing chamber. Sophisticated sensors and data acquisition systems provide precise measurements, ensuring that the process adheres to established protocols. Deviations from set parameters are immediately flagged, allowing for prompt adjustments or process intervention. This proactive approach helps maintain consistency and mitigate potential issues. For example, in a steel heat-treating facility, continuous monitoring of furnace temperature is crucial for consistent material hardness. Discrepancies detected through monitoring systems enable immediate intervention, preventing inconsistent outcomes.
- Material Characterization
Post-treatment analysis of the material is vital for verifying the effectiveness of the deep heat treatment. Techniques like metallographic analysis, hardness testing, and tensile testing provide concrete evidence that the material properties meet the specified requirements. Comparing results to pre-defined benchmarks and specifications ensures that the process meets quality standards. This approach, common in automotive manufacturing, confirms that components exhibiting the correct hardness and toughness are produced consistently.
- Process Documentation and Audit Trails
Maintaining comprehensive documentation of the entire process is crucial. Detailed records of temperature profiles, time durations, and specific material characteristics are essential for traceability and process validation. Regular audits of these records, procedures, and equipment help ensure compliance with industry standards and regulatory requirements. In pharmaceutical manufacturing, documentation of every step of the sterilization process is imperative. Audit trails verify that procedures are consistently followed and help trace any deviations or potential issues.
- Statistical Process Control (SPC)
Applying statistical methods to monitor process variations is a key element of quality assurance. SPC charts track key process variables, facilitating identification of trends or anomalies. Early detection of deviations from the norm enables timely corrective actions. This methodology, particularly important in manufacturing processes, helps prevent costly issues that might arise from inconsistencies or deviations during deep heat treatments, ensuring the final product adheres to stringent quality standards. For instance, in a semiconductor fabrication plant, SPC helps manage temperature variations during diffusion processes.
Ultimately, comprehensive quality assurance in deep heat treatment provides confidence in the reliability and consistency of the final product. Implementing these procedures is essential for maintaining quality control, improving process efficiency, and safeguarding against potential production issues and safety risks. Consistent adherence to QA practices ensures the product's efficacy and reliability, directly impacting performance and longevity, particularly important in critical applications. The robust standards employed in the QA process provide confidence in the material's performance and suitability for the intended use.
Frequently Asked Questions about Deep Heat Treatment
This section addresses common queries regarding deep heat treatment, providing concise and informative answers. The questions cover key aspects of the process, including technical details and practical implications.
Question 1: What distinguishes deep heat treatment from other thermal processes?
Deep heat treatment is distinguished by its focus on achieving specific, targeted material alterations through highly controlled temperature and time parameters. It differs from general heating processes by the intense precision in manipulating temperature gradients, heating and cooling rates, and the duration of exposure to elevated temperatures. This focused approach allows for precise control over the material's microstructure and resultant properties, leading to enhancements in strength, hardness, ductility, and other characteristics not typically achievable through simpler heating methods.
Question 2: What are the critical factors influencing the success of deep heat treatment?
Several factors influence the success of deep heat treatment. Material properties, such as thermal conductivity and chemical composition, dictate the optimal treatment parameters. Precise temperature control, encompassing careful monitoring of gradients and heating/cooling rates, is critical. Accurate time durations for specific temperature profiles are essential. Finally, the design of the treatment process itself plays a pivotal role in obtaining the desired outcome. Proper equipment calibration is also essential.
Question 3: What are the typical applications of deep heat treatment?
Deep heat treatment finds diverse applications across various industries. It's crucial in manufacturing high-performance alloys used in aerospace, automotive, and other industries that require components with enhanced strength and durability. Deep heat treatment is also employed in semiconductor manufacturing, food preservation, and other sectors requiring meticulously controlled material alteration for specific outcomes.
Question 4: What are the potential risks or limitations of deep heat treatment?
Potential risks include material distortion, unwanted phase transformations, and the development of internal stresses if parameters are not precisely controlled. Incorrectly calibrated equipment can lead to inaccurate temperature profiles, ultimately compromising the quality of the heat-treated material. Furthermore, some materials might exhibit reduced ductility or increased brittleness if subjected to inappropriate heat treatment conditions.
Question 5: How can the effectiveness of deep heat treatment be evaluated?
The effectiveness of deep heat treatment is evaluated through a variety of methods, including material analysis techniques (e.g., metallographic analysis), mechanical property testing (e.g., hardness testing, tensile testing), and visual inspection. These procedures verify if the material characteristics meet specified requirements and standards. Comparision to pre-treatment data provides a definitive measure of the treatment's success.
These FAQs provide a foundational understanding of deep heat treatment. Further research into specific applications or materials may offer more detailed insights.
Conclusion
This exploration of deep heat treatment methodologies highlights the intricate interplay of various factors. Precise temperature control, calibrated equipment, and meticulous process design are critical for achieving the desired material transformations. The specific characteristics of the treated material, including its thermal conductivity and chemical composition, directly influence the effectiveness and outcome of the process. Maintaining consistent and predictable results hinges on adhering to established quality assurance protocols and implementing statistical process controls. The importance of material analysis, process documentation, and rigorous monitoring underscores the need for comprehensive understanding and control throughout the entire deep heat treatment procedure.
Deep heat treatment is a complex process with far-reaching applications in diverse sectors, including aerospace, automotive, and semiconductor manufacturing. Continued advancements in this field, driven by innovations in equipment technology, materials science, and process optimization, promise to unlock further potential and enhance the properties of materials for improved performance and durability in a wide array of applications. Future research and development should focus on developing more sustainable and efficient deep heat treatment methods while maintaining exacting quality standards.
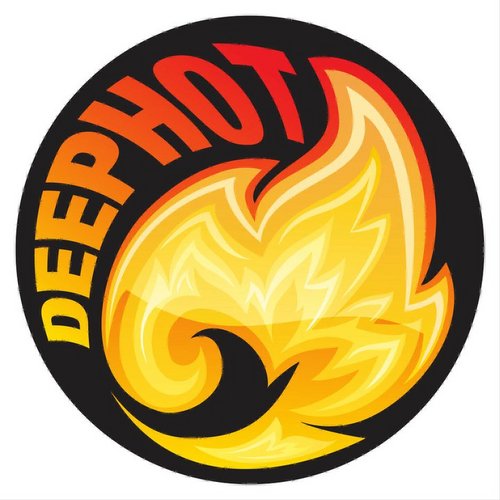
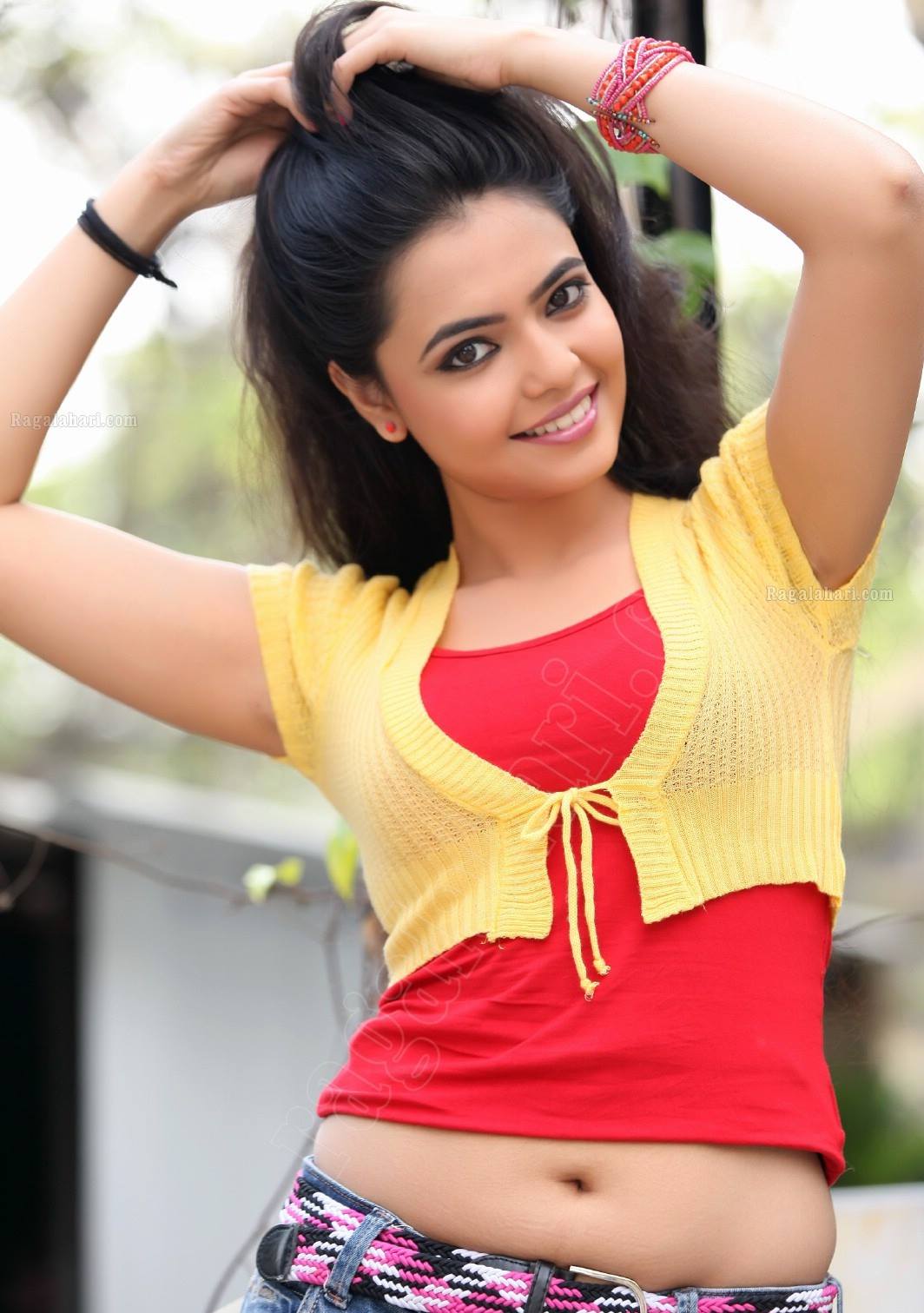
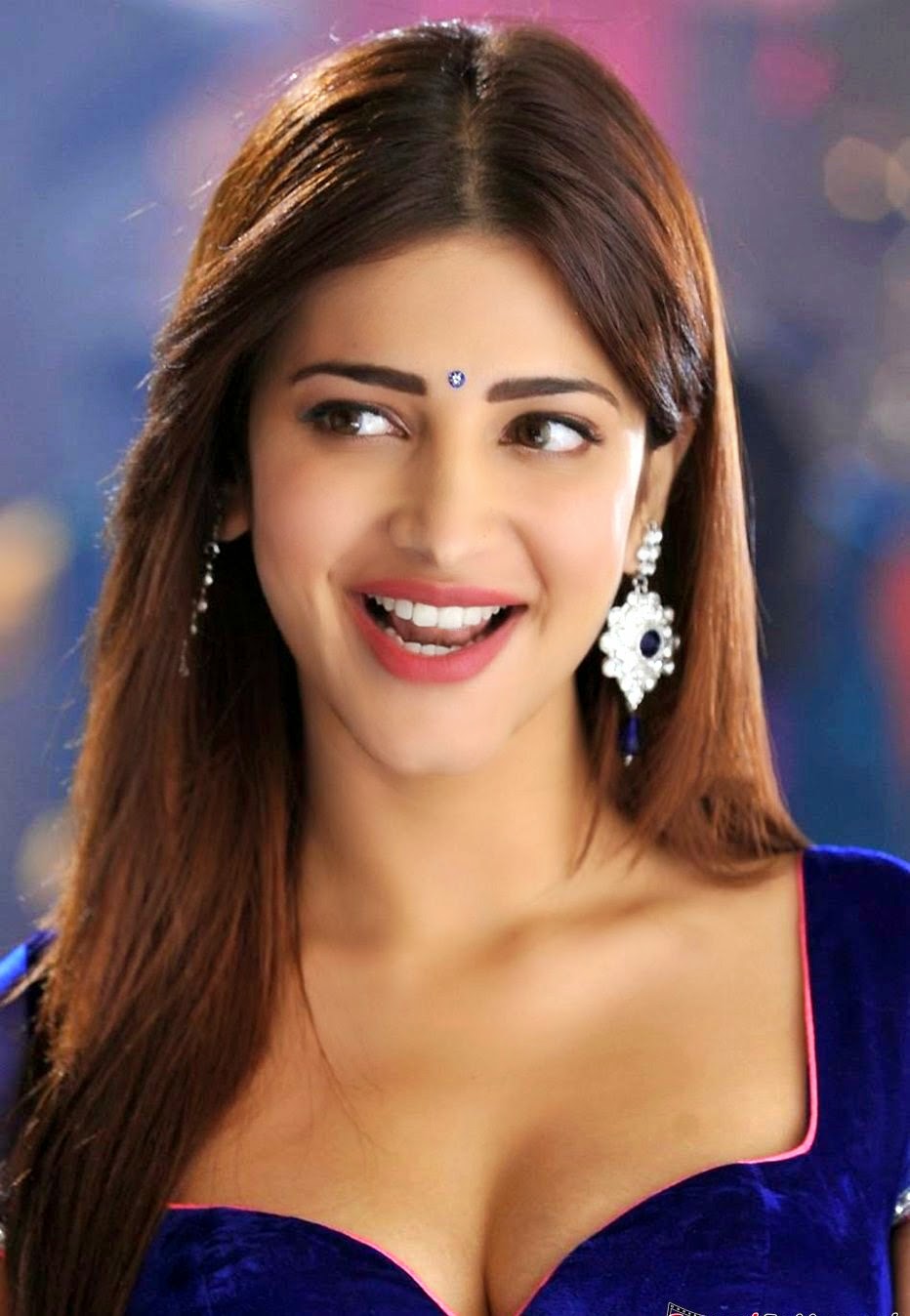
Detail Author:
- Name : Laurie Runolfsdottir
- Username : viviane.harber
- Email : linnie.hodkiewicz@bogan.com
- Birthdate : 1993-09-27
- Address : 516 Waters Plains North Timothy, VA 33515
- Phone : +16825049230
- Company : Dare Ltd
- Job : Mathematical Scientist
- Bio : Eum quaerat dolorem consequuntur repellat quod quia. Qui praesentium autem voluptatem. Id aut neque pariatur et eius nisi.
Socials
twitter:
- url : https://twitter.com/eric.harber
- username : eric.harber
- bio : Recusandae perferendis quam enim. Quia blanditiis omnis laborum tempora provident. Totam dicta debitis ex fugiat accusantium expedita velit.
- followers : 6425
- following : 1898
linkedin:
- url : https://linkedin.com/in/eric_harber
- username : eric_harber
- bio : Fugit natus rerum est a quia ullam.
- followers : 1311
- following : 1024
facebook:
- url : https://facebook.com/harber2008
- username : harber2008
- bio : Autem maxime labore sit ipsam. Non incidunt debitis dolores sint maiores est.
- followers : 1693
- following : 1254